135.堿石灰燒結(jié)法的原理是什么?
答:堿石灰燒結(jié)法生產(chǎn)氧化鋁是將鋁土礦與一定數(shù)量的蘇打石灰(或石灰石)配成爐料,在回轉(zhuǎn)窯內(nèi)進(jìn)行高溫?zé)Y(jié),爐料中的A2lO3與Na2CO3反應(yīng)生成可溶性的固體鋁酸鈉。雜質(zhì)氧化鐵、二氧化硅和二氧化鈦分別生成鐵酸鈉、原硅酸鈣和鈦酸鈣。這些化合物都是在熟料中能夠同時保持平衡的。鋁酸鈉極易溶于水或稀堿溶液,鐵酸鈉則易水解。而原硅酸鈣和鈦酸鈣不溶于水,與堿溶液的反應(yīng)也較微弱。因此,稀堿溶液溶出時,可以將熟料中的Al2O3和Na2O溶出,得到鋁酸鈉溶液,與進(jìn)入赤泥的硅酸鈣、鈦酸鈣和赤鐵礦等不溶性殘渣分離。熟料的溶出液(粗液)經(jīng)過專門的脫硅凈化過程得到純凈的鋁酸鈉精液。它在通入CO2氣體后,苛性比值和穩(wěn)定性降低,于是析出氫氧化鋁并得到碳分Na,CO母液,后者經(jīng)蒸發(fā)濃縮后返回配料。因此在生產(chǎn)過程中Na2CO3也是循環(huán)使用的。
136.堿石灰燒結(jié)法的基本流程是怎樣的?
答:堿石灰燒結(jié)法制備氫氧化鋁的基本流程圖如圖2-3所示。
137.氧化鋁生產(chǎn)對原料制備的要求有哪些?
答:氧化鋁生產(chǎn)對原料制備的要求有:(1)參與化學(xué)反應(yīng)的物料要有一定的細(xì)度;(2)參與化學(xué)反應(yīng)的物料各成分之間要有一定的配比并充分混合。原料制備在氧化鋁生產(chǎn)中具有重要的作用。能否制備出滿足氧化鋁生產(chǎn)要求的生料漿,將直接影響氧化鋁及氧化鈉的溶出率,也影響熟料窯的操作等。
138.燒結(jié)過程的目的和要求分別是什么?
答:燒結(jié)過程的主要目的在于將生料中的A2lO3盡可能完全地轉(zhuǎn)變成可溶性的鋁酸鈉、氧化鐵轉(zhuǎn)變成鐵酸鈉,而雜質(zhì)SiO2、TiO2轉(zhuǎn)變?yōu)椴蝗苄缘脑杷徕}和鈦酸鈣。燒結(jié)過程所得到的熟料具有適當(dāng)?shù)膹?qiáng)度和可磨性。
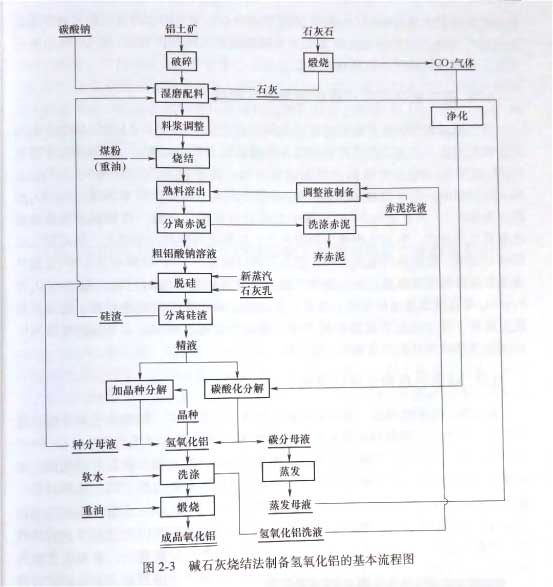
熟料粒度應(yīng)該均勻,大塊的出現(xiàn)是燒結(jié)溫度過高的標(biāo)志,而粉末太多則是欠燒的結(jié)果。熟料大部分應(yīng)為30~50mm,呈灰黑色,無熔結(jié)或夾帶欠燒的現(xiàn)象。
139.燒結(jié)過程中主要的物理化學(xué)反應(yīng)有哪些?
答:燒結(jié)過程中主要的物化反應(yīng)有:(1)Al2O3與Na2CO3生成偏鋁酸鈉。(2)用燒結(jié)法處理高硅含鋁原料時,爐料中的SiO在燒結(jié)過程中應(yīng)該轉(zhuǎn)變?yōu)楣杷徕}。SiO2和CaO可以生成CaO· SiO2(偏硅酸鈣)、3CaO 2SiO(二硅酸三鈣)、2CaO·SiO2(原硅酸鈣)、3CaO·SiO2(硅酸三鈣)四種化合物。只有原硅酸鈣在高溫下能與Na20 AL2O3同時穩(wěn)定存在,而且溶出時不與鋁酸鈉溶液生顯著的反應(yīng)。(3)氧化鐵在高溫下與碳酸鈉反應(yīng)生成鐵酸鈉。(4)TiO2參與反應(yīng),生成鈣鈦礦進(jìn)入熟料和溶出渣。
140.硫?qū)ρ趸X生產(chǎn)造成的危害有哪些?
答:硫?qū)ρ趸X生產(chǎn)造成的危害主要有以下幾個方面:(1)生料中含有的硫使堿耗增加。進(jìn)入生產(chǎn)流程中的硫與堿液反應(yīng)生成Na2SO4。而Na2SO4不能與Al203起反應(yīng),稱為中性堿,增加堿耗。1kg硫大約損失NaOH1~1.5kg或Na2CO3 3.4kg。(2)熟料中的Na2SO4含量升高對大窯操作帶來困難。Na2SO4的熔點為884℃,并且能與NaCO等生成熔點較低的化合物,使物料進(jìn)入燒成帶之前就出現(xiàn)液相。Na2SO4熔體的黏度較大,易使?fàn)t料黏掛在窯壁上,結(jié)成厚的副窯壁和結(jié)圈,致使熟料滾成大球,造成下料口堵塞。(3)母液Na2SO4含量升高給蒸發(fā)操作帶來困難,并且增加氣耗。分解母液在蒸發(fā)時若有大量Na2SO4和Na2SO3等在蒸發(fā)器加熱管壁上結(jié)晶析出,則會降低管壁的傳熱系數(shù),使蒸發(fā)器能力顯著下降。并且蒸發(fā)器結(jié)疤嚴(yán)重,清洗次數(shù)隨之增加。(4)拜耳精液中Na2SO4含量增加,將使分解率有所下降。
141.燒結(jié)過程如何進(jìn)行排硫?
答:混聯(lián)法和燒結(jié)法主要采取生料加煤技術(shù)進(jìn)行排硫。燒結(jié)法生料加煤,能夠脫除大量的硫,具有穩(wěn)定熟料窯操作的作用,并且還有以下優(yōu)點:(1)一部分Fe2O3被還原為FeO,配料時可以適當(dāng)減少Na2O配人量,從而節(jié)約用堿。如果配堿量不變,則相應(yīng)地提高堿比,從而提高Al2O3的溶出率。(2)生料加煤后燒制的熟料在正常情況下熟料中S2~含量大于0.32%,Na2SO4么含量穩(wěn)定在2%以下,可獲得黑心多孔、可磨性好的熟料,因此可改善熟料在濕磨過程中的粉碎性質(zhì),熟料溶出產(chǎn)能可提高8%~10%。(3)因不易產(chǎn)生過磨現(xiàn)象,溶出后赤泥為黑綠色,細(xì)度均勻適中,改善了赤泥沉降性能,提高了沉降槽的產(chǎn)能,同時可降低溶出過程二次反應(yīng)損失。
142.影響熟料質(zhì)量的主要因素有哪些?
答:(1)爐料成分。爐料成分決定著熟料的物相成分,如果爐料不符合配方要求,在熟料中便不能生成預(yù)期的物相,而使Al2O3、Na2O的溶出率降低。爐料成分對于燒結(jié)溫度和燒結(jié)溫度范圍也有影響。
(2)燒結(jié)溫度。適宜的燒結(jié)溫度主要決定于爐料成分。當(dāng)燒結(jié)溫度過低時化學(xué)反應(yīng)進(jìn)行不完全,因而使熟料中的Al2O3和Na2O溶出率降低。同時由于存在著未反應(yīng)的游離石灰,在赤泥分離過程增加出現(xiàn)赤泥膨脹的可能性。溶出液與赤泥接觸的時間延長,使得Al2O3、Na2O的損失增加。當(dāng)燒結(jié)溫度過高時,熟料過燒使窯的作業(yè)失常,不僅使煤耗增加,窯的產(chǎn)能降低,濕磨產(chǎn)能降低,而且由于堿的揮發(fā),導(dǎo)致熟料成分的改變,也使有用成分的溶出率下降。
(3)煤粉質(zhì)量。燒結(jié)爐料的回轉(zhuǎn)窯所用的燃料一般為煙煤煤粉,煤粉中含有大量的灰分,有時還有相當(dāng)數(shù)量的硫化物?;曳种饕葾l2O3、SiO2、CaO和Fe2O3組成。而且SiO2的含量常常在50%以上。灰分中各成分直接落在爐料中與蘇打、石灰反應(yīng)。因此配料時必須考慮進(jìn)入熟料中灰分的數(shù)量及其組成。
(4)爐料的粒度和混合程度。爐料燒結(jié)時的物理化學(xué)反應(yīng)是在固態(tài)下進(jìn)行的,僅在結(jié)束時有少量熔體出現(xiàn),因而物料的細(xì)磨程度對反應(yīng)速度和反應(yīng)完全程度是有影響的。
143.燒結(jié)中為什么會產(chǎn)生燒結(jié)結(jié)圈,結(jié)圈對燒結(jié)產(chǎn)生哪些影響?
答:生料燒結(jié)過程中,由于液相的出現(xiàn)和凝結(jié),在燒成帶前后兩端形成致密而高于窯皮的結(jié)圈稱為前結(jié)圈和后結(jié)圈。
氧化鋁熟料中2CaO·SiO和NaOFeO是生成液相的主要成分,其次是MgO、NaSO等雜質(zhì)。隨著配料中鋁硅比(A/S)的降低,熟料的熔融溫度顯著降低,燒成范圍窄,出現(xiàn)結(jié)圈的機(jī)會多。當(dāng)其他成分一定時,鋁硅比(A/S)小于2.8時結(jié)圈顯著增加,鋁硅比(A/S)大于3.2時結(jié)圈可緩和或生成的結(jié)圈不致造成危害;當(dāng)FeO含量增多,F(xiàn)/A大于0.15時,結(jié)圈會產(chǎn)生;當(dāng)堿比小于0.9時會導(dǎo)致結(jié)圈的生成;喂料不均,料層不均使火焰位置伸長或縮短交換的頻繁改變,也會加速結(jié)圈生成;燃料中含硫高也會使結(jié)圈增多。
結(jié)圈對熟料窯的生產(chǎn)影響很大,一般它高于正常窯皮1~2倍,非正常狀態(tài)下,甚至高出窯皮3~4倍。它既影響熟料窯的穩(wěn)定操作及技術(shù)經(jīng)濟(jì)指標(biāo),又影響熟料窯的長期安全運轉(zhuǎn)。因為結(jié)圈使窯內(nèi)通風(fēng)面積縮小,導(dǎo)致通風(fēng)不良;破壞窯的熱工制度,嚴(yán)重時無法操作;威脅安全生產(chǎn),如造成電收塵爆炸事故,因此,要盡量防止結(jié)圈的生成,生成后則要及時消除。
144.鋁酸鹽熟料的溶出的目的和要求分別是什么?
答:熟料溶出過程要使熟料中的NaOAlO盡可能完全地轉(zhuǎn)入溶液,而NayO·Fe,O盡可能完全地分解,以獲得AlO、NaO高的溶出率。溶出液要與赤泥盡快地分離,以減少氧化鋁和堿的化學(xué)損失。分離后的赤泥,夾帶著附液,應(yīng)充分洗滌,以減少堿和氧化鋁的機(jī)械損失。
145.熟料溶出過程中的主要反應(yīng)有哪些?
答:燒結(jié)法熟料中主要成分是鋁酸鈉、鐵酸鈉、原硅酸鈣。在熟料溶出過程中,鋁酸鈉溶解在堿溶液中,鐵酸鈉水解生成氫氧化鈉進(jìn)入溶液,含水氧化鐵進(jìn)入赤泥,化學(xué)反應(yīng)式為:
Na20·Al203+4H20→2NaAl(OH)4 (2-5)
Na20·Fe203+2H20→2NaOH+Fe2O3·H2O↓ (2-6)
原硅酸鈣除少量被溶液中的氫氧化鈉、碳酸鈉、鋁酸鈉分解,使二氧化硅進(jìn)人溶液外,大部分殘留在固體殘渣中。
146.鋁酸鈉溶液脫硅過程有什么意義和要求?
答:熟料在溶出過程中,由于2CaOSiO2與溶液中的NaOH、Na2CO3及NaAl(OH)4。相互作用而被分解,使較多的二氧化硅進(jìn)入溶液。通常在熟料溶出液中,Al2O3濃度約為120g/L,SiO2含量高達(dá)4.5~6g/L,高出鋁酸鈉溶液中SiO2平衡濃度許多倍,這種SiO2過飽和程度很高的粗液,在碳酸化分解過程中,大部分SiO2將隨氫氧化鋁一起析出,使產(chǎn)品氧化鋁不符合質(zhì)量要求。因此,在進(jìn)行分解以前,粗液必須經(jīng)過專門的脫硅過程。一般要求精液的硅量指數(shù)大于400。目前國內(nèi)外燒結(jié)法廠已經(jīng)發(fā)展了多種脫硅流程,例如,先在溫度為150~170℃的壓煮器中進(jìn)行一段脫硅,使溶液中硅量指數(shù)提高到400左右,然后再在常壓下加石灰進(jìn)行二段脫硅,使溶液硅量指數(shù)達(dá)到1000~1500。
147.什么是二次脫硅?
答:在一次脫硅漿液從脫硅機(jī)經(jīng)自蒸發(fā)器進(jìn)入緩沖槽時,再加入石灰乳進(jìn)行脫硅,使殘存的SiO2以水化石榴石析出,該工藝稱為二次脫硅,二次脫硅所得精液硅量指數(shù)可提高到1000~1500以上。二次脫硅工藝之所以可以達(dá)到較好的脫硅效果,是因為在高溫并加硅渣作晶種的一次脫硅條件下,粗液中大部分SiO2 在脫硅機(jī)中以鈉硅渣析出。這時再加入石灰乳,石灰乳與溶液及SiO2反應(yīng),生成溶解度更小的水化石榴石固相,使溶液中的SiO2含量進(jìn)一步降低,提高了脫硅的深度。
148.什么叫深度脫硅?
答:深度脫硅也稱為三次脫硅,是指在現(xiàn)有的二次脫硅工藝的精液中再添加少量的石灰乳在反應(yīng)槽中反應(yīng)1~1.5h。鈣硅渣分離后返回二次脫硅工序。深度脫硅的基本原理與二次脫硅基本相同。深度脫硅所生成的水化石榴石中SiO2的飽和度比較低,一般為0.1g/L左右。
149.影響脫硅過程的主要因素有哪些?
答:(1)溫度。溫度對脫硅過程的動力學(xué)有決定性作用。在100~170℃范圍內(nèi),隨著溫度的升高水合鋁硅酸鈉結(jié)晶析出的速度顯著提高,溶解度降低,硅量指數(shù)不斷提高。在壓力大于0.7MPa時溶液的鋁硅比(A/S)最高。繼續(xù)提高溫度,由于SiO2的溶解度復(fù)而增大,溶液的鋁硅比(A/S)反而降低,適當(dāng)?shù)靥岣邷囟瓤梢钥s短脫硅時間,增大設(shè)備產(chǎn)能,因而生產(chǎn)中多采用加壓脫硅。
(2)原液中Al2O3的濃度。精液中SiO平衡濃度隨Al2O3(Na2O)濃度的降低而降低。因此降低Al2O3濃度有利于制得硅量指數(shù)較高的精液。
(3)原液Na2O濃度。保持溶液中Al3O2濃度不變,提高Na2O濃度,即提高其苛性比值,使得SiO2的平衡濃度提高,硅量指數(shù)顯著降低。因此,在保證溶液有足夠穩(wěn)定性的前提下,苛性比值越低,脫硅效果越好。
(4)原液中 Na2CO3、Na2SO4和 NaCl 的濃度。粗液中往往含有一定量的Na2CO3和Na2SO4等鹽類,它們屬于水合硅酸鈉核心所吸收的附加鹽,可以生成
3(Na2O·Al2O3·2SiO2·2H2O)·Na(2)X·nH2O一類沸石族化合物,分子式中X 代表CO2-3、SO2-4、Cl-、Al(OH)-4等陰離子。由于這一類沸石族化合物在鋁酸鈉溶液中的溶解度均小于Na2O·Al2O3·2SiO2·2H2O的溶解度,因此,這些鹽類的存在可以降低SiO2的平衡濃度,提高脫硅深度的影響。
(5)添加晶種。添加適量晶種可以避免水合鋁硅酸鈉形成晶核的困難,促使脫硅深度和速度顯著地提高。
(6)脫硅時間。當(dāng)溫度一定,二氧化硅沒有達(dá)到平衡前,溶液的硅量指數(shù)隨著時間延續(xù)而提高。不過時間越長,反應(yīng)速度越慢,硅量指數(shù)增長速度越慢。
150.赤泥分離的主要目的是什么?
答:赤泥分離的主要目的是使熟料中的氧化鋁、氧化鈉盡可能地轉(zhuǎn)入溶液,以獲得較高的溶出率。使溶液與不溶物盡快分離,減少氧化鋁和氧化鈉的化學(xué)損失,并將合格的粗液送去脫硅。
151.赤泥洗滌的主要目的是什么,為什么采用反向洗滌?
答:經(jīng)赤泥分離后得到的赤泥,都帶有一定數(shù)量的附著液。為了回收赤泥附液中的有用成分Al2O3和Na2O,赤泥必須用熱水加以洗滌,一般需要經(jīng)過5~8 次熱水反向洗滌,以盡可能回收氧化鋁和氧化鈉,減少其機(jī)械損失。
在赤泥洗滌中,采用熱水與赤泥流向相反的工藝流程,可以減少熱水消耗,提高洗滌效率,獲得較高的濃度的赤泥洗液,返回生產(chǎn)流程。
152.碳酸化分解的目的和要求分別是什么?
答:碳酸化分解是將脫硅后的精液通入CO2,使NaOH轉(zhuǎn)變成為碳酸鈉,促使氫氧化鋁從溶液中洗出來,得到的氫氧化鋁和主要成分為碳酸鈉的碳分母液,后者經(jīng)蒸發(fā)濃縮后返回配制生料漿,氫氧化鋁則在洗滌煅燒后成為氧化鋁。
碳酸化分解作業(yè),必須在保證產(chǎn)品質(zhì)量的前提下,盡可能地提高分解率和分解槽的產(chǎn)能,極力減少隨同碳分母液送去配制生料漿的Al2O3量,借以降低整個流程中的物料流量和有用成分的損失。
153.碳酸化分解的原理是怎樣的?
答:碳酸化分解是同時存在氣液固三相的多相反應(yīng)過程。發(fā)生的物理化學(xué)反應(yīng)包括:(1)二氧化碳為鋁酸鈉溶液吸收,使苛性堿中和;(2)氫氧化鋁的析出;(3)水合鋁硅酸鈉的結(jié)晶析出;(4)水合碳鋁酸鈉(Na20·Al2O3·2CO2·nH2O)的生成和破壞,并在碳酸化分解終了時沉淀析出。水合鋁硅酸鈉的析出主要是在碳分過程的末期,它使氫氧化鋁被SiO2和堿污染。碳酸化分解末期當(dāng)溶液中剩下Al2O3少于2~3g/L時,由于溶液溫度不高,使水合碳酸鈉生成析出。所以,當(dāng)溶液徹底碳酸化分解時,所得氫氧化鋁中含有大量的碳酸鈉。
154.碳酸化分解方法有哪幾種?
答:根據(jù)具體條件及對產(chǎn)品質(zhì)量要求的不同,碳酸化分解方法也不一樣,主要有以下幾種:
(1)完全碳酸化。這種方法是將鋁酸鈉溶液碳酸化至氧化鋁全部析出。該方法到目前為止,工業(yè)上還沒有采用過。
(2)分段碳酸化。這種方法是使鋁酸鈉溶液中的氫氧化鋁分段析出。(3)混合分解法。這種方法是將精液先部分地進(jìn)行碳酸化,然后將溶液繼續(xù)進(jìn)行種子分解。
155.影響碳酸化分解過程的主要因素有哪些?
答:(1)分解原液的純度和碳酸化分解深度。分解原液的純度包括硅量指數(shù)和浮游物兩個方面。分解原液浮游物是Al(OH)3中雜質(zhì)SiO2,和Na2O的來源之一,是雜質(zhì)Fe2O3的最主要來源。碳酸化分解率主要根據(jù)精液的硅量指數(shù)和氫氧化鋁中SiO2允許量來確定的,硅量指數(shù)越高,在保證氫氧化鋁質(zhì)量的前提下,其他條件相同時,濃度較高的精液要比濃度較低的精液分解的氫氧化鋁中的SiO2 和不可洗去的堿多。
(2)CO2氣體的純度、濃度和通氣速度。CO2氣體的濃度及通氣速度決定著分解的速率,高濃度的CO2氣源,分解速率快。分解槽產(chǎn)能以及CO2利用率高,有利于氫氧化鋁晶體長大,節(jié)省壓縮機(jī)動力。當(dāng)CO2氣體壓力一定時,達(dá)到預(yù)定分解率時,通氣時間短,則通氣速度越快。同時,提高通氣速度,縮短了分解時間,并使分解出的Al(OH)3迅速地與母液分離,可以減少SiO2的析出數(shù)量。
(3)分解溫度。分解溫度高,有利于氫氧化鋁晶體的長大,從而可減弱其吸附堿和二氧化硅的能力,并有利于氫氧化鋁的分離和洗滌。
(4)晶種。在精液中加入適量的氫氧化鋁晶種,提高碳酸化分解初期的分解率,還能改善碳分Al(OH)3的晶體結(jié)構(gòu)和粒度組成,降低Al(OH)3的雜質(zhì)SiO2和Na2O含量,使其粒度均勻,同時能減少槽內(nèi)結(jié)垢程度。晶種的加入使氫氧化鋁循環(huán)積壓于流程中,增加了氫氧化鋁分離設(shè)備的負(fù)擔(dān)。
(5)攪拌。攪拌可使溶液成分均勻,避免局部碳酸化,并有利于晶種的生長,得到粒度較粗和堿含量較低的氫氧化鋁;此外,攪拌還可以減輕碳分槽內(nèi)的結(jié)垢和沉淀。
156.如何提高碳分槽的產(chǎn)能和質(zhì)量?
答:提高碳分槽產(chǎn)能和質(zhì)量的方法有:(1)提高硅量指數(shù)A/S。降低精液中雜質(zhì)SiO2含量,提高硅量指數(shù)。精液中SiO2。含量越低,分解率越高,這樣可提高產(chǎn)量和Al(OH)3質(zhì)量,降低消耗。(2)降低氫氧化鋁水分,降低熱耗為了降低焙燒窯的熱耗,把過濾機(jī)的單真空頭改為雙真空頭,連續(xù)吹風(fēng)改為間接吹風(fēng)。減少氫氧化鋁附著水,可降低焙燒窯油耗。(3)降低Al(OH)3中的附堿量。為了降低Al(OH)3中的附堿量,我國燒結(jié)法工廠的氫氧化鋁過濾機(jī)采用二次反向洗滌,洗滌水量為1t Al(OH)3用1~1.2t水,水溫大于90℃,為了進(jìn)一步提高Al(OH)3質(zhì)量,降低附堿量,也采用三次反向洗滌,但不利于生產(chǎn)能耗的降低。(4)提高分解槽產(chǎn)能。通過加強(qiáng)技術(shù)操作和設(shè)備改造,提高分解槽的產(chǎn)能。選擇合理的分解周期、溶液濃度及苛性比值、CO2壓力和濃度、分解率等指標(biāo)。對攪拌鏈板進(jìn)行加固以保證安全運轉(zhuǎn),加大汽水分離器,周期性地清除結(jié)疤,防止阻塞管道而造成冒槽,以及將進(jìn)料系統(tǒng)閥門改轉(zhuǎn)壺,主要是縮短進(jìn)料時間,減輕勞動強(qiáng)度,這些都有利于提高分解槽的產(chǎn)能。
157.碳分槽的基本結(jié)構(gòu)是什么?
答:碳酸化分解是在碳分槽內(nèi)進(jìn)行的。碳分槽的主體結(jié)構(gòu)如圖2-4所示。通常碳分槽是用鋼板焊接而成的圓筒形槽體,內(nèi)裝有掛鏈?zhǔn)降臋C(jī)械攪拌器,槽壁裝有4根從槽的下部通入CO2氣體的支管。
158.什么是連續(xù)碳酸化分解工藝,其有什么特點?
答:連續(xù)碳酸化分解是在一組(一般為6臺)碳分槽內(nèi)連續(xù)進(jìn)行的碳酸化分解作業(yè),每個碳分槽都保持一定的操作條件。連續(xù)碳酸化分解,保持了碳酸化分解生產(chǎn)流程的連續(xù)化,設(shè)備利用率、產(chǎn)能和勞動生產(chǎn)率均高于間斷碳酸化分解,提高了設(shè)備生產(chǎn)能力,減輕了勞動強(qiáng)度,而且還能防止分解槽的結(jié)疤生成,生產(chǎn)過程較易實現(xiàn)自動化。但存在產(chǎn)品Al(OH)3粒度較細(xì)、含堿量較高、動力消耗大的問題。
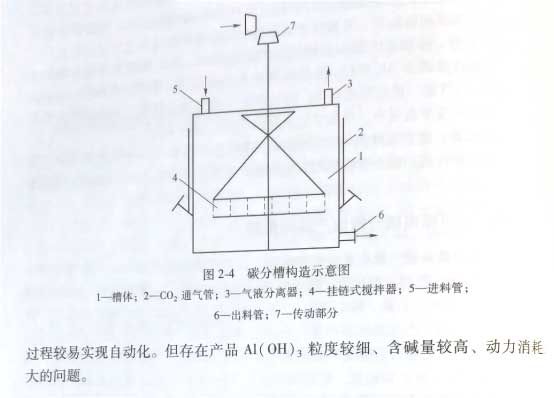
159.分解母液蒸發(fā)器的結(jié)垢原因是什么,如何減少結(jié)垢的產(chǎn)生?
答:氧化硅在母液中的含量是過飽和的,它以鋁硅酸鈉形態(tài)析出的速度隨溫度的升高而加快。但它在鋁酸鈉溶液中的溶解度隨Na2O濃度增加而增加。因此低濃度的鋁酸鈉母液在蒸發(fā)過程中,隨著水分的蒸發(fā),水合鋁硅酸鈉析出并在加熱管壁上結(jié)垢。
防止和減輕蒸發(fā)器結(jié)垢的方法很多,除了將導(dǎo)致結(jié)垢的雜質(zhì)組分預(yù)先從生產(chǎn)流程中排出和采用適當(dāng)?shù)恼舭l(fā)流程和作業(yè)條件以外,還可以采用物理化學(xué)方法。近年來,國內(nèi)外對于采用磁場、電場、超聲波以及使用添加劑等方法預(yù)防氧化鋁生產(chǎn)設(shè)備的結(jié)垢進(jìn)行了很多研究。例如,在適當(dāng)條件下在電場中處理蒸發(fā)母液,可大大減輕乃至完全防止在加熱面上生產(chǎn)鋁硅酸鈉結(jié)垢,從而可使蒸發(fā)器產(chǎn)能提高20%。