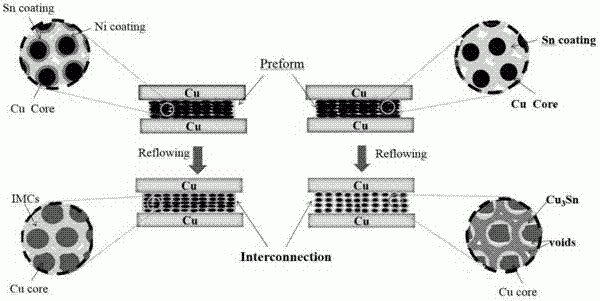
本發(fā)明涉及一種cu@ni@sn預(yù)成型焊片及其制備方法。
背景技術(shù):
電力電子模塊在電動(dòng)汽車、航空航天、軌道交通等方面的使用越來(lái)越廣泛。第三代寬禁帶半導(dǎo)體如sic,因具有高熔點(diǎn)、高功率密度,以及優(yōu)越的導(dǎo)熱導(dǎo)電性能成為替代si
芯片的最優(yōu)材料,要發(fā)揮sic芯片的優(yōu)越性能,耐高溫的芯片焊接材料和焊接技術(shù)是關(guān)鍵和制約因素。
傳統(tǒng)的高溫焊接材料包括au-sn,bi-ag-xsn-xpb、sn-pb-ag。因au、ag貴金屬成本高,焊接溫度在280~330℃,影響溫度敏感元器件性能;隨著歐盟對(duì)pb等有毒金屬限制條令的頒布,焊pb器件及產(chǎn)品逐步退出市場(chǎng)。雖然對(duì)電力電子產(chǎn)品給出了豁免期限,但高溫?zé)o鉛替代產(chǎn)品及焊接材料研發(fā)已迫在眉睫。
目前研究較多的高溫?zé)o鉛焊接材料包括燒結(jié)納米銀技術(shù)及cu/sn、ni/sn或au/sn的瞬時(shí)液相擴(kuò)散焊(tlp)技術(shù)等。納米銀燒結(jié)焊接技術(shù)相比于其他幾種技術(shù)具有比較優(yōu)異的高溫性能。但是,該技術(shù)不僅需要較高的成本,而且納米銀容易遷移,導(dǎo)致空洞率較高,同時(shí),其焊接工藝與傳統(tǒng)的焊接技術(shù)不兼容,導(dǎo)致應(yīng)用受到限制。
瞬時(shí)液相擴(kuò)散焊接(tlp)技術(shù)利用低熔點(diǎn)金屬(如sn、in等)與兩側(cè)高熔點(diǎn)金屬(如cu、ni、au等)形成三明治結(jié)構(gòu),回流過(guò)程,低熔點(diǎn)金屬熔化,與高熔點(diǎn)金屬發(fā)生固液互擴(kuò)散,形成完全界面金屬間化合物的焊接界面。利用這種焊接技術(shù)的焊接層厚度一般小于20μm,不利于吸收因芯片及基板等系統(tǒng)材料熱膨脹系數(shù)適配產(chǎn)生的熱應(yīng)力,難以滿足電力電子器件高可靠封裝的需要。中國(guó)專利cn100475996c公開(kāi)了一種高溫?zé)o鉛焊料用組合物、生產(chǎn)方法及元件,該無(wú)鉛高溫焊料包含一種含銀2wt%-18wt%、含鉍98wt%-82wt%的銀鉍合金,具有固相線不低于262.5℃、液相線不高于400℃,但是,該無(wú)鉛焊料用組合物強(qiáng)度和塑性較低,此焊料用普通助焊膏做成的錫膏在抗坍塌能力較差,錫珠較多,不利于該無(wú)鉛焊料用組合物的工業(yè)化生產(chǎn)和推廣。cn104476007a公開(kāi)了一種高熔點(diǎn)無(wú)鉛無(wú)鹵焊錫膏及其制備方法,該焊錫膏焊料合金具有固相線溫度高于260℃以上,具有強(qiáng)度高,塑性高,抗疲勞特性強(qiáng)的優(yōu)點(diǎn),助焊膏具有優(yōu)良的防坍塌功能該技術(shù)是一種非常具有實(shí)用前景的可與傳統(tǒng)焊膏工藝相兼容的高溫;中國(guó)專利cn101234456a公開(kāi)了一種錫銀金無(wú)鉛焊接材料及其制備方法,其熔化溫度可達(dá)到300℃,潤(rùn)濕性和電學(xué)性能優(yōu)良,焊接效果良好,可代替?zhèn)鹘y(tǒng)的sn-95%pb焊料合金。其組成為銀8~13%、金35~45%,其余為錫。貴金屬用量大,成本高,焊接溫度高;專利cn104588906a公開(kāi)了一種sn-cu高溫?zé)o鉛焊膏及其制備方法和使用方法,該焊膏焊接的樣品使用溫度可高達(dá)400℃,焊縫剪切強(qiáng)度高,性能穩(wěn)定,但該技術(shù)仍然沿用的是焊膏,需要采用容易產(chǎn)生污染的絲網(wǎng)印刷工藝;由于焊接過(guò)程,焊接材料不能潤(rùn)濕鋪展,因此,焊膏揮發(fā)后留下大面積的孔洞,接頭疏松,影響導(dǎo)熱效率及可靠性。
技術(shù)實(shí)現(xiàn)要素:
本發(fā)明的目的是為了克服上述現(xiàn)有技術(shù)的不足,致力于研發(fā)環(huán)保、低成本、高可靠的高溫焊料,提出一種核殼結(jié)構(gòu)cu@ni@sn無(wú)鉛焊片及其制備方法。所述cu@ni表示ni包覆cu,cu@ni@sn表示sn包ni包c(diǎn)u,其中,cu是內(nèi)核,ni為中間包覆層,sn為包覆外層。
本發(fā)明核殼結(jié)構(gòu)cu@ni@sn無(wú)鉛焊片成型體積密度為4000kg/m3~6000kg/m3,厚度為100~400μm,焊接溫度240℃-270℃,保溫時(shí)間6~10min。焊接后接頭抗拉伸強(qiáng)度>220mpa,-70℃~200℃高溫循環(huán)200個(gè)周期,每個(gè)循環(huán)周期約36分鐘,高溫循環(huán)后剪切強(qiáng)度約為80mpa,焊接后焊件的使用溫度高達(dá)400℃。本發(fā)明焊片可以在較低的工藝溫度下實(shí)現(xiàn)焊接,接頭耐受>415℃的高溫重熔。
本發(fā)明核殼結(jié)構(gòu)cu@ni@sn焊接材料由cu顆粒、ni鍍層及sn鍍層組成,其中cu顆粒為內(nèi)核,ni鍍層為內(nèi)層殼,sn鍍層為外層殼。所述的銅顆粒粒徑為5~20μm,ni鍍層厚度為0.5~1μm;sn鍍層厚度為1~3μm或3~5μm;所述ni鍍層和sn鍍層均采用化學(xué)鍍工藝制備。
核殼結(jié)構(gòu)cu@ni@sn粉末按照cu核粒徑的大小分為三種尺度:5~10μm,10~15μm及15~20μm,分別記為小、中、大三種粒徑。為使焊片致密,三種粒徑粉末按照3:2:1的比例配置后機(jī)械混合,充分?jǐn)嚢?。為使焊片與基板界面充分互聯(lián),焊片分為上中下三層:上層和下層的厚度均為50~80μm;中間層為粉末,厚度為320~350μm。焊片上層和下層為與基板的接觸側(cè),焊片上層和下層采用sn鍍層厚度為3~5μm的cu@ni@sn核殼結(jié)構(gòu)粉末;焊片的中間層采用sn鍍層厚度為1~3μm的cu@ni@sn核殼結(jié)構(gòu)粉末。
本發(fā)明核殼結(jié)構(gòu)cu@ni@sn焊片的制備方法包括如下步驟:
(1)將不同粒徑的銅顆粒置于niso4的化學(xué)鍍液中反應(yīng)5~15min后,獲得均勻鍍覆一層0.5~1μmni鍍層的cu@ni,將cu@ni粉末放置于snso4化學(xué)鍍液中,反應(yīng)10~30min后,在ni鍍層表面均勻鍍覆一層1~3μm或3~5μm的sn層,獲得兩種sn鍍層的cu@ni@sn核殼結(jié)構(gòu)粉末;
(2)分別將步驟(1)制備的,sn鍍層厚度為1~3μm和3~5μm的cu@ni@sn雙核粉末,按照大、中、小粒徑1:2:3的比例配比,放置于混料機(jī)中,在100~300r/min速率下,機(jī)械混合1~2h,得到sn鍍層厚度不同兩種均勻混合粉末;
(3)將步驟(2)制得的,其中sn鍍層厚度為3~5μm雙核粉末置于壓片磨具的上、下兩層,將步驟(2)制得的sn鍍層厚度為1~3μm雙核粉末置于壓片磨具的中間層,上層和下層的厚度均為50~80μm,中間層厚度為320~350μm;
(4)將步驟(3)制備的三層粉體在高壓壓片機(jī)上壓力成型,壓片機(jī)壓力范圍為10~30mpa,得到厚度為100~400μm的cu@ni@sn復(fù)合預(yù)成型焊片。
對(duì)所述的復(fù)合預(yù)成型焊片進(jìn)行后續(xù)的低溫液相擴(kuò)散焊接,利用sn的低熔點(diǎn),使得焊片本體相在較低的焊接工藝溫度下,利用cu與sn的液固反應(yīng)轉(zhuǎn)化為耐高溫的cu6sn5/cu3sn界面金屬間化合物,由于少量ni鍍層的存在,有效抑制cu的過(guò)量消耗生成cu3sn。
回流焊接時(shí),將焊接體系“基板/焊片/芯片”放置在陶瓷加熱板上,在真空或惰性氣體氣氛中,于240℃~270℃下熱處理6~10min,隨爐冷卻。焊接結(jié)束后,焊片本體相經(jīng)xrd分析,測(cè)得的物相成分為cu、cu6sn5、cu3sn與ni3sn4等物相的混合相。經(jīng)拉伸試驗(yàn)機(jī)測(cè)試,得到接頭的拉伸強(qiáng)度>220mpa;于-70~200℃的高溫下循環(huán)200周期后接頭剪切強(qiáng)度不低于80mpa。
所述焊片焊接后,在250℃下時(shí)效200h后接頭組織依然致密,主要物相為cu、cu6sn5,少量cu3sn與ni3sn4,cu3sn的熔點(diǎn)為415℃,cu6sn5的熔點(diǎn)為676℃,ni3sn4的熔點(diǎn)為794.5℃。因此,利用該焊片焊接后的焊件使用溫度可高達(dá)400℃以上。
與現(xiàn)有技術(shù)相比,本發(fā)明的有益效果是:
1)用本發(fā)明的雙核焊片焊接金屬材料時(shí),焊接瞬間有液相金屬sn產(chǎn)生,焊接結(jié)束時(shí)sn層完全轉(zhuǎn)化為產(chǎn)生金屬間化合物,形成界金屬?gòu)?qiáng)化cu顆粒的三維網(wǎng)絡(luò)結(jié)構(gòu)接頭。cu6sn5和cu3sn熔點(diǎn)分別為415℃和676℃,ni3sn4的熔點(diǎn)為794.5℃,從而保證接頭材料耐溫大于400℃。
2)本發(fā)明焊片的焊接溫度為240-270℃,采用本焊片焊接焊件后,焊縫在工作溫度低于400℃時(shí)不會(huì)熔化失效,焊縫可經(jīng)受高達(dá)400℃的高溫工作環(huán)境。
3)本發(fā)明的雙核焊片實(shí)現(xiàn)了焊料合金化與焊接過(guò)程的統(tǒng)一,且為無(wú)鉛錫基焊片,環(huán)保、工藝簡(jiǎn)單、成本低。
4)本發(fā)明雙核焊接粉末采用金屬cu的電鍍工藝,不需要金屬熔融成合金再霧化的方式,不僅使得制備方法簡(jiǎn)單,而且有助于降低焊接溫度,當(dāng)焊片達(dá)到錫熔解的溫度即可焊接。
5)本發(fā)明的雙核高溫焊接粉末,由于ni阻擋層的存在,cu顆粒在高溫時(shí)效及服役過(guò)程不會(huì)被過(guò)度消耗,保證了接頭結(jié)構(gòu)的致密性和接頭性能的穩(wěn)定性。
6)本發(fā)明的雙核高溫焊片采用的原材料cu、ni、sn,成本低、導(dǎo)電導(dǎo)熱性能優(yōu)異,且sn鍍層延展性好,從而使cu@ni@sn復(fù)合焊片易于成型,并且在焊接過(guò)程使cu顆粒間通過(guò)界面金屬間化合物實(shí)現(xiàn)致密連接。
7)本cu@ni@sn雙核焊片特別適用于電力電子領(lǐng)域耐高溫電子元器件。
附圖說(shuō)明
圖1單核cu@sn與雙核cu@ni@sn組織結(jié)構(gòu)對(duì)比示意圖;
圖2本發(fā)明cu@ni@sn焊片的的致密三維網(wǎng)絡(luò)接頭微觀組織形貌;
圖3雙核cu@ni@sn與單核cu@sn焊片焊接前后的物相成分分析;
圖4回流焊接接頭與高溫溫度循環(huán)接頭的剪切強(qiáng)度對(duì)比。
具體實(shí)施方式
圖1為單核cu@sn與雙核cu@ni@sn預(yù)成型焊片及焊接接頭的組織結(jié)構(gòu)示意對(duì)比圖。如圖1所示,單核cu@sn與雙核cu@ni@sn在一定的壓力下形成的預(yù)成型焊片組織差異不大,孔隙率相似,但經(jīng)過(guò)回流焊接之后,單核的三維網(wǎng)絡(luò)結(jié)構(gòu)出現(xiàn)了柯肯達(dá)爾孔洞,而雙核cu@ni@sn焊料形成的接頭微觀組織致密,其對(duì)比示意圖如圖1所示。經(jīng)時(shí)效處理后,單核接頭結(jié)構(gòu)孔洞體積增大,而雙核接頭致密性變化不大。
實(shí)施例1
采用粒度為5~10μm與10~15μm的銅粉,分別電鍍制備ni和sn鍍層:將不同粒徑的銅顆粒置于niso4的化學(xué)鍍液中反應(yīng)5min后,獲得均勻鍍覆一層0.5μmni鍍層的cu@ni,將cu@ni粉末放置于snso4化學(xué)鍍液中,反應(yīng)10min后,在ni鍍層表面均勻鍍覆一層3.0μm的sn層,獲得兩種sn鍍層的cu@ni@sn雙核粉末。對(duì)不同sn鍍層厚度的兩種粉末分別按照3:2的比例進(jìn)行粒度級(jí)配,將級(jí)配后的粉末置于高速球磨機(jī)中,在100r/min速率下機(jī)械混合1h,得到sn層厚度分別為1.0μm和3.0μm的均勻混合復(fù)合粉末。
稱取上述sn層厚度為3.0μm的混合粉末0.02g分別放置于壓片磨具的上下兩層,稱取上述sn層厚為1.0μm混合粉體0.09g置于磨具中間層,在壓力為10mpa的壓力機(jī)上進(jìn)行高壓壓片,恒壓時(shí)間10min,得到厚度為389μm的復(fù)合預(yù)成型焊片;
將所述的復(fù)合預(yù)成型焊片在240℃下進(jìn)行低溫液相擴(kuò)散焊接,低熔點(diǎn)sn熔化瞬間分別于ni和cu發(fā)生固液擴(kuò)散反應(yīng)生成cu6sn5與ni3sn4界面金屬間化合物,6分鐘回流結(jié)束后,sn鍍層全部轉(zhuǎn)化為界面金屬間化合物,cu@sn焊接材料與cu@ni@sn焊接材料焊接前后的物相成分如圖3所示。
實(shí)施例2
采用粒度為5~10μm與15~20μm的銅粉,分別電鍍制備ni和sn鍍層:將不同粒徑的銅顆粒置于niso4的化學(xué)鍍液中反應(yīng)10min后,獲得均勻鍍覆一層0.6μmni鍍層的cu@ni,將cu@ni粉末放置于snso4化學(xué)鍍液中,反應(yīng)20min后,在ni鍍層表面均勻鍍覆一層厚度分別為1.5μm和3.5μm的sn層,獲得兩種sn鍍層厚度的cu@ni@sn雙核粉末。對(duì)不同sn鍍層厚度的兩種粉末分別按照3:1的比例進(jìn)行粒度級(jí)配,將級(jí)配后的粉末置于高速球磨機(jī)中,在200r/min速率下機(jī)械混合2h,得到sn層厚度分別為1.5μm和3.5μm的均勻混合復(fù)合粉末。
稱取上述sn層厚度為3.5μm的混合粉末0.01g分別放置于壓片磨具的上下兩層,稱取上述sn層厚為1.5μm混合粉體0.12g,置于磨具中間層,在壓力為15mpa的壓力機(jī)上進(jìn)行高壓壓片,恒壓時(shí)間10min,得到厚度為380μm的復(fù)合預(yù)成型焊片;
所述的復(fù)合預(yù)成型焊片在270℃下進(jìn)行低溫液相擴(kuò)散焊接,低熔點(diǎn)的sn熔化瞬間分別于ni和cu發(fā)生固液擴(kuò)散反應(yīng)生成cu6sn5與ni3sn4界面金屬間化合物,8分鐘回流結(jié)束后,sn鍍層全部轉(zhuǎn)化為界面金屬間化合物,其三維網(wǎng)絡(luò)結(jié)構(gòu)的界面微觀組織如圖2所示。
實(shí)施例3
采用粒度為10~15μm與15~20μm的銅粉,分別電鍍制備ni和sn鍍層:將不同粒徑的銅顆粒置于niso4的化學(xué)鍍液中反應(yīng)15min后,獲得均勻鍍覆一層0.7μmni鍍層的cu@ni,將cu@ni粉末放置于snso4化學(xué)鍍液中,反應(yīng)30min后,在ni鍍層表面均勻鍍覆一層厚度分別為2.0μm和3.5μm的sn層,獲得兩種sn鍍層的cu@ni@sn雙核粉末。對(duì)不同sn鍍層厚度的兩種粉末分別按照2:1的比例進(jìn)行粒度級(jí)配,將級(jí)配后的粉末置于高速球磨機(jī)中,在300r/min速率下機(jī)械混合2h,得到sn層厚度分別為2.0μm和3.5μm的均勻混合復(fù)合粉末。
稱取上述sn層厚度為3.5μm的混合粉末0.03g分別放置于壓片磨具的上下兩層,稱取上述sn層厚為1.5μm混合粉體0.10g,置于磨具中間層,在壓力為20mpa的壓力機(jī)上進(jìn)行高壓壓片,恒壓時(shí)間10min,得到厚度為395μm的復(fù)合預(yù)成型焊片;
將所述的復(fù)合預(yù)成型焊片在260℃下進(jìn)行低溫液相擴(kuò)散焊接,低熔點(diǎn)的sn熔化瞬間分別于ni和cu發(fā)生固液擴(kuò)散反應(yīng)生成cu6sn5與ni3sn4界面金屬間化合物,8分鐘回流結(jié)束后,sn鍍層全部轉(zhuǎn)化為界面金屬間化合物。
實(shí)施例4
采用粒度為5~10μm、10~15μm與15~20μm的銅粉,分別進(jìn)行電鍍ni和電鍍sn鍍層制備:將不同粒徑的銅顆粒置于niso4的化學(xué)鍍液中反應(yīng)12min后,獲得均勻鍍覆一層0.8μmni鍍層的cu@ni,將cu@ni粉末放置于snso4化學(xué)鍍液中,反應(yīng)25min后,在ni鍍層表面均勻鍍覆一層厚度分別為2.0μm和3.5μm的sn層,獲得兩種sn鍍層的cu@ni@sn雙核粉末。對(duì)不同sn鍍層厚度的兩種粉末分別按照3:2:1的比例進(jìn)行粒度級(jí)配將級(jí)配后的粉末置于高速球磨機(jī)中,在300r/min速率下機(jī)械混合2h,得到sn層厚度分別為2.0μm和3.5μm均勻混合復(fù)合粉末。
稱取上述sn層厚度為3.5μm的混合粉末0.04g分別放置于壓片磨具的上下兩層,稱取上述sn層厚為2.0μm混合粉體0.09g,置于磨具中間層,在壓力為20mpa的壓力機(jī)上進(jìn)行高壓壓片,恒壓時(shí)間10min,得到厚度為380μm的復(fù)合預(yù)成型焊片;
將所述的復(fù)合預(yù)成型焊片在270℃下進(jìn)行低溫液相擴(kuò)散焊接,低熔點(diǎn)的sn熔化瞬間分別于ni和cu發(fā)生固液擴(kuò)散反應(yīng)生成cu6sn5與ni3sn4界面金屬間化合物,10分鐘回流結(jié)束后,sn鍍層全部轉(zhuǎn)化為界面金屬間化合物,其焊接接頭剪切強(qiáng)度高達(dá)220mpa,但于-70~200℃溫度區(qū)間循環(huán)200周期后剪切強(qiáng)度降至80mpa,如圖4所示,接頭依然具有較好的機(jī)械支撐作用。
實(shí)施例5
采用粒度為5~10μm的銅粉,分別進(jìn)行電鍍制備ni和sn鍍層:將不同粒徑的銅顆粒置于niso4的化學(xué)鍍液中反應(yīng)12min后,獲得均勻鍍覆一層0.9μmni鍍層的cu@ni,將cu@ni粉末放置于snso4化學(xué)鍍液中,反應(yīng)22min后,在ni鍍層表面均勻鍍覆一層厚度分別為2.8μm和4.0μm的sn層,獲得兩種sn鍍層的cu@ni@sn雙核粉末。對(duì)不同sn鍍層厚度的兩種粉末分別置于高速球磨機(jī)中,在300r/min速率下機(jī)械混合2h,得到sn層厚度分別為2.8μm和4.0μm均勻混合復(fù)合粉末。
稱取上述sn層厚度為4.0μm的混合粉末0.03g分別放置于壓片磨具的上下兩層,稱取上述sn層厚為2.8μm混合粉體0.12g,置于磨具中間層,在壓力為20mpa的壓力機(jī)上進(jìn)行高壓壓片,恒壓時(shí)間10min,得到厚度為378μm的復(fù)合預(yù)成型焊片;
將所述的復(fù)合預(yù)成型焊片在250℃下進(jìn)行低溫液相擴(kuò)散焊接,低熔點(diǎn)的sn熔化瞬間分別于ni和cu發(fā)生固液擴(kuò)散反應(yīng)生成cu6sn5與ni3sn4界面金屬間化合物,8分鐘回流結(jié)束后,sn鍍層全部轉(zhuǎn)化為界面金屬間化合物,其焊接前后的物相成分如圖3所示。
實(shí)施例6
采用粒度為5~20μm的銅粉,分別進(jìn)行電鍍制備ni和電鍍sn層:將不同粒徑的銅顆粒置于niso4的化學(xué)鍍液中反應(yīng)15min后,獲得均勻鍍覆一層1.0μmni鍍層的cu@ni,將cu@ni粉末放置于snso4化學(xué)鍍液中,反應(yīng)30min后,在ni鍍層表面均勻鍍覆一層厚度分別為3.0μm和5.0μm的sn層,獲得兩種sn鍍層的cu@ni@sn雙核粉末。對(duì)不同sn鍍層厚度的兩種粉末分別置于高速球磨機(jī)中,在300r/min速率下機(jī)械混合1h,得到sn層厚度分別為3.0μm和5.0μm均勻混合復(fù)合粉末。
稱取上述sn層厚度為5.0μm的混合粉末0.02g分別放置于壓片磨具的上下兩層,稱取上述sn層厚為3.0μm混合粉體0.11g,置于磨具中間層,在壓力為20mpa的壓力機(jī)上進(jìn)行高壓壓片,恒壓時(shí)間10min,得到厚度為388μm的復(fù)合預(yù)成型焊片;
將所述的復(fù)合預(yù)成型焊片在250℃下進(jìn)行低溫液相擴(kuò)散焊接,低熔點(diǎn)的sn熔化瞬間分別于ni和cu發(fā)生固液擴(kuò)散反應(yīng)生成cu6sn5與ni3sn4界面金屬間化合物,8分鐘回流結(jié)束后,sn鍍層全部轉(zhuǎn)化為界面金屬間化合物,其焊接前后的物相成分如圖3所示。
技術(shù)特征:
技術(shù)總結(jié)
一種Cu@Ni@Sn預(yù)成型焊接材料,由Cu顆粒、Ni鍍層及Sn鍍層組成。所述Cu顆粒粒徑為5~20μm,Ni鍍層的厚度為0.5~1μm,Sn鍍層的厚度為1~5μm。Cu@Ni@Sn核殼結(jié)構(gòu)粉末用化學(xué)鍍工藝制備。該預(yù)成型焊片制備方法如下:1)按照3:2:1的比例稱取不同粒徑:5~10μm、10~15μm及15~20μm的Cu@Ni@Sn核殼結(jié)構(gòu)微球,其中Sn鍍層厚度分別為1~3μm和3~5μm;2)將所配制的兩種Sn鍍層厚度的Cu@Ni@Sn微球分別置于混料機(jī)中,在100~300r/min速率下,機(jī)械混合1~2h,得到Sn鍍層厚度不同的兩種均勻混合粉末;3)將一定質(zhì)量Sn鍍層厚度大的粉末放置于壓片磨具的上下兩側(cè),一定質(zhì)量Sn鍍層厚度小的放置于磨具中間,在自動(dòng)壓片機(jī)上壓力成型,壓片機(jī)壓力范圍為10~20MPa,得到厚度為100~400μm的Cu@Ni@Sn核殼結(jié)構(gòu)預(yù)成型焊片。
技術(shù)研發(fā)人員:徐紅艷;徐菊
受保護(hù)的技術(shù)使用者:中國(guó)科學(xué)院電工研究所
技術(shù)研發(fā)日:2018.09.14
技術(shù)公布日:2019.01.11

1.本發(fā)明涉及再生砂技術(shù)領(lǐng)域,具體為一種陶瓷砂輪再生砂制作方法。
背景技術(shù):
2.陶瓷砂輪用配比好的陶瓷結(jié)合劑把磨粒粘結(jié)起來(lái),經(jīng)壓坯、干燥、焙燒及修整而成的,具有很多氣孔、用磨粒進(jìn)行切削的磨具。磨粒以其露在表面部分的尖角作為切削刃。因此陶瓷砂輪在鉆石、工業(yè)陶瓷、金剛石復(fù)合片,金剛石聚晶,金剛石刀具,立方氮化硼,硬質(zhì)合金等高硬脆材料等一些特殊材料的磨削加工中,具有越來(lái)越明顯的優(yōu)勢(shì),在金剛石磨具的發(fā)展中有著良好的前景。被認(rèn)為是高速、高效、高精、低磨削成本、低環(huán)境污染的高性能磨具,具有越來(lái)越廣泛的應(yīng)用,是世界各國(guó)磨削工具競(jìng)相研究開(kāi)發(fā)的熱點(diǎn)。
3.陶瓷砂輪在加工過(guò)程中會(huì)呈現(xiàn)許多廢品,而這些廢品不能再次利用,而且陶瓷砂輪當(dāng)磨損超出負(fù)荷后,并處于報(bào)廢狀態(tài),因此廢舊的陶瓷砂輪數(shù)量隨著時(shí)間而增加,為了提高陶瓷砂輪的利用,我們提出了一種陶瓷砂輪再生砂制作方法。
技術(shù)實(shí)現(xiàn)要素:
4.針對(duì)現(xiàn)有技術(shù)存在的上述不足,本發(fā)明提供了一種陶瓷砂輪再生砂制作方法。
5.本發(fā)明提供如下技術(shù)方案:一種陶瓷砂輪再生砂制作方法,包括以下操作:
6.s1、破碎處理
7.將廢舊陶瓷砂輪內(nèi)孔部位的灌孔材料砸掉,然后去清除其他雜質(zhì),再將廢舊陶瓷砂輪經(jīng)
破碎機(jī)破碎,之后投入球磨機(jī)內(nèi)進(jìn)行粉碎,得到粉末;
8.s2、篩分處理
9.將經(jīng)球磨的粉末進(jìn)行篩分,其他較大砂粒重新導(dǎo)入球磨機(jī)再次粉碎,直至達(dá)標(biāo)為止;
10.s3、清洗處理
11.將粉末導(dǎo)入酸性溶劑中進(jìn)行清洗,之后取出在清水中進(jìn)行漂洗,最后通過(guò)高溫將表面雜質(zhì)清除,并進(jìn)行干燥處理;
12.s4、成型
13.將粉末與氯化鎂液、菱苦土粉、糊精粉和石英石粉末混合,并放入模具中進(jìn)行壓制成型,并將毛坯樣品放入高溫爐中,進(jìn)行燒制,燒成后待其自然冷卻后,便可取出;
14.s5、成品
15.將產(chǎn)品取出,并經(jīng)破碎機(jī)將其碎成塊狀,之后導(dǎo)入球磨機(jī)內(nèi)進(jìn)行研磨,形成再生砂。
16.優(yōu)選的,所述廢舊陶瓷砂輪在破碎之前需要經(jīng)過(guò)超聲波清洗,干燥后進(jìn)行破碎。
17.優(yōu)選的,所述砂粒的研磨標(biāo)準(zhǔn)為60
?
120目。
18.優(yōu)選的,所述清洗時(shí),粉末需要全部浸入酸性溶劑中,之后通過(guò)過(guò)濾的方式,將粉末濾出,且水洗過(guò)程相同。
19.優(yōu)選的,所述壓制成型時(shí),壓力保持在8mpa,并保持壓力3分鐘后,才能取出。
20.優(yōu)選的,所述毛坯樣品在壓制成形后,需要進(jìn)行干燥處理,將毛坯中多余的水分清除。
21.與現(xiàn)有技術(shù)對(duì)比,本發(fā)明具備以下有益效果:
22.該陶瓷砂輪再生砂制作方法,通過(guò)廢砂輪進(jìn)行破碎、加工處理,制出顆粒,并加入各種材料進(jìn)行再生,制得的再生砂具有良好的耐磨性能和硬度,有利用資源的回收再利用,工藝簡(jiǎn)單,成品合格率高,且再生砂可進(jìn)行回收處理進(jìn)行恢復(fù)。
具體實(shí)施方式
23.為了使本公開(kāi)實(shí)施例的目的、技術(shù)方案和優(yōu)點(diǎn)更加清楚,因此,對(duì)本公開(kāi)實(shí)施例的技術(shù)方案進(jìn)行清楚、完整地描述,為了保持本公開(kāi)實(shí)施例的以下說(shuō)明清楚且簡(jiǎn)明,本公開(kāi)省略了已知功能和已知部件的詳細(xì)說(shuō)明,以避免不必要地混淆本發(fā)明的概念。
24.實(shí)施例1
25.一種陶瓷砂輪再生砂制作方法,包括以下操作:
26.將廢舊陶瓷砂輪內(nèi)孔部位的灌孔材料砸掉,然后去清除其他雜質(zhì),并經(jīng)過(guò)超聲波清洗,之后進(jìn)行干燥處理,再將廢舊陶瓷砂輪經(jīng)破碎機(jī)破碎,之后投入球磨機(jī)內(nèi)進(jìn)行粉碎,得到粉末;
27.將經(jīng)球磨的粉末進(jìn)行篩分,其他較大砂粒重新導(dǎo)入球磨機(jī)再次粉碎,直至60
?
120目為止;
28.將粉末導(dǎo)入酸性溶劑中進(jìn)行清洗,之后取出在清水中進(jìn)行漂洗,粉末需要全部浸入酸性溶劑中,之后通過(guò)過(guò)濾的方式,將粉末濾出,且水洗過(guò)程相同,最后通過(guò)高溫將表面雜質(zhì)清除,并進(jìn)行干燥處理;
29.將粉末與氯化鎂液、菱苦土粉、糊精粉和石英石粉末混合,并放入模具中進(jìn)行壓制成型,壓力保持在8mpa,并保持壓力3分鐘后取出,然后進(jìn)行干燥處理,將毛坯中多余的水分清除,最后將毛坯樣品放入高溫爐中,進(jìn)行燒制,燒成后待其自然冷卻后,便可取出;
30.將產(chǎn)品取出,并經(jīng)破碎機(jī)將其碎成塊狀,之后導(dǎo)入球磨機(jī)內(nèi)進(jìn)行研磨,形成再生砂。
31.實(shí)施例2
32.一種陶瓷砂輪再生砂制作方法,包括以下操作:
33.將廢舊陶瓷砂輪內(nèi)孔部位的灌孔材料砸掉,然后去清除其他雜質(zhì),并經(jīng)過(guò)超聲波清洗,之后進(jìn)行干燥處理,再將廢舊陶瓷砂輪經(jīng)破碎機(jī)破碎,之后投入球磨機(jī)內(nèi)進(jìn)行粉碎,得到粉末;
34.將經(jīng)球磨的粉末進(jìn)行篩分,其他較大砂粒重新導(dǎo)入球磨機(jī)再次粉碎,直至達(dá)標(biāo)為止;
35.將粉末導(dǎo)入酸性溶劑中進(jìn)行清洗,之后取出在清水中進(jìn)行漂洗,粉末需要全部浸入酸性溶劑中,之后通過(guò)過(guò)濾的方式,將粉末濾出,且水洗過(guò)程相同,最后通過(guò)高溫將表面雜質(zhì)清除,并進(jìn)行干燥處理;
36.將粉末與氯化鎂液、菱苦土粉、糊精粉和石英石粉末混合,并放入模具中進(jìn)行壓制成型,然后進(jìn)行干燥處理,將毛坯中多余的水分清除,最后將毛坯樣品放入高溫爐中,進(jìn)行
燒制,燒成后待其自然冷卻后,便可取出;
37.將產(chǎn)品取出,并經(jīng)破碎機(jī)將其碎成塊狀,之后導(dǎo)入球磨機(jī)內(nèi)進(jìn)行研磨,形成再生砂。
38.實(shí)施例3
39.一種陶瓷砂輪再生砂制作方法,包括以下操作:
40.將廢舊陶瓷砂輪內(nèi)孔部位的灌孔材料砸掉,然后去清除其他雜質(zhì),并經(jīng)過(guò)超聲波清洗,之后進(jìn)行干燥處理,再將廢舊陶瓷砂輪經(jīng)破碎機(jī)破碎,之后投入球磨機(jī)內(nèi)進(jìn)行粉碎,得到粉末,將經(jīng)球磨的粉末進(jìn)行篩分,其他較大砂粒重新導(dǎo)入球磨機(jī)再次粉碎,直至達(dá)標(biāo)為止;
41.將粉末導(dǎo)入酸性溶劑中進(jìn)行清洗,之后取出在清水中進(jìn)行漂洗,粉末需要全部浸入酸性溶劑中,之后通過(guò)過(guò)濾的方式,將粉末濾出,且水洗過(guò)程相同,最后通過(guò)高溫將表面雜質(zhì)清除,并進(jìn)行干燥處理;
42.將粉末與氯化鎂液、菱苦土粉、糊精粉和石英石粉末混合,并放入模具中進(jìn)行壓制成型,最后將毛坯樣品放入高溫爐中,進(jìn)行燒制,燒成后待其自然冷卻后,便可取出,將產(chǎn)品取出,并經(jīng)破碎機(jī)將其碎成塊狀,之后導(dǎo)入球磨機(jī)內(nèi)進(jìn)行研磨,形成再生砂。
43.實(shí)驗(yàn)
[0044][0045]
綜上所述,該再生砂各個(gè)方便均符合標(biāo)準(zhǔn)。
[0046]
以上實(shí)施例僅為本發(fā)明的示例性實(shí)施例,不用于限制本發(fā)明,本發(fā)明的保護(hù)范圍由權(quán)利要求書(shū)限定。本領(lǐng)域技術(shù)人員可以在本發(fā)明的實(shí)質(zhì)和保護(hù)范圍內(nèi),對(duì)本發(fā)明做出各種修改或等同替換,這種修改或等同替換也應(yīng)視為落在本發(fā)明的保護(hù)范圍內(nèi)。
技術(shù)特征:
1.一種陶瓷砂輪再生砂制作方法,其特征在于,包括以下操作:s1、破碎處理將廢舊陶瓷砂輪內(nèi)孔部位的灌孔材料砸掉,然后去清除其他雜質(zhì),再將廢舊陶瓷砂輪經(jīng)破碎機(jī)破碎,之后投入球磨機(jī)內(nèi)進(jìn)行粉碎,得到粉末;s2、篩分處理將經(jīng)球磨的粉末進(jìn)行篩分,其他較大砂粒重新導(dǎo)入球磨機(jī)再次粉碎,直至達(dá)標(biāo)為止;s3、清洗處理將粉末導(dǎo)入酸性溶劑中進(jìn)行清洗,之后取出在清水中進(jìn)行漂洗,最后通過(guò)高溫將表面雜質(zhì)清除,并進(jìn)行干燥處理;s4、成型將粉末與氯化鎂液、菱苦土粉、糊精粉和石英石粉末混合,并放入模具中進(jìn)行壓制成型,并將毛坯樣品放入高溫爐中,進(jìn)行燒制,燒成后待其自然冷卻后,便可取出;s5、成品將產(chǎn)品取出,并經(jīng)破碎機(jī)將其碎成塊狀,之后導(dǎo)入球磨機(jī)內(nèi)進(jìn)行研磨,形成再生砂。2.根據(jù)權(quán)利要求1所述的一種陶瓷砂輪再生砂制作方法,其特征在于:所述廢舊陶瓷砂輪在破碎之前需要經(jīng)過(guò)超聲波清洗,干燥后進(jìn)行破碎。3.根據(jù)權(quán)利要求1所述的一種陶瓷砂輪再生砂制作方法,其特征在于:所述砂粒的研磨標(biāo)準(zhǔn)為60
?
120目。4.根據(jù)權(quán)利要求1所述的一種陶瓷砂輪再生砂制作方法,其特征在于:所述清洗時(shí),粉末需要全部浸入酸性溶劑中,之后通過(guò)過(guò)濾的方式,將粉末濾出,且水洗過(guò)程相同。5.根據(jù)權(quán)利要求1所述的一種陶瓷砂輪再生砂制作方法,其特征在于:所述壓制成型時(shí),壓力保持在8mpa,并保持壓力3分鐘后,才能取出。6.根據(jù)權(quán)利要求1所述的一種陶瓷砂輪再生砂制作方法,其特征在于:所述毛坯樣品在壓制成形后,需要進(jìn)行干燥處理,將毛坯中多余的水分清除。
技術(shù)總結(jié)
本發(fā)明涉及再生砂技術(shù)領(lǐng)域,且公開(kāi)了一種陶瓷砂輪再生砂制作方法,包括以下操作:將廢舊陶瓷砂輪內(nèi)孔部位的灌孔材料砸掉,然后去清除其他雜質(zhì),再將廢舊陶瓷砂輪經(jīng)破碎機(jī)破碎,之后投入球磨機(jī)內(nèi)進(jìn)行粉碎,得到粉末;將經(jīng)球磨的粉末進(jìn)行篩分,其他較大砂粒重新導(dǎo)入球磨機(jī)再次粉碎,直至達(dá)標(biāo)為止。該陶瓷砂輪再生砂制作方法,通過(guò)廢砂輪進(jìn)行破碎、加工處理,制出顆粒,并加入各種材料進(jìn)行再生,制得的再生砂具有良好的耐磨性能和硬度,有利用資源的回收再利用,且工藝簡(jiǎn)單,成品合格率高。成品合格率高。
技術(shù)研發(fā)人員:宋學(xué)立 郭軍霞 郭軍義
受保護(hù)的技術(shù)使用者:臨沂茂源
新材料科技有限公司
技術(shù)研發(fā)日:2021.10.11
技術(shù)公布日:2021/12/10
聲明:
“陶瓷砂輪再生砂制作方法與流程” 該技術(shù)專利(論文)所有權(quán)利歸屬于技術(shù)(論文)所有人。僅供學(xué)習(xí)研究,如用于商業(yè)用途,請(qǐng)聯(lián)系該技術(shù)所有人。
我是此專利(論文)的發(fā)明人(作者)