隨著河南氧化鋁內(nèi)鋰、鉀、鈣含量的不斷增多,從2008年下半年開始我廠516臺300kA預(yù)焙電解槽槽溫度不斷下降,截止2014年底槽溫度由2008年初的平均963℃下降到905℃,下降了58℃,初晶溫度不斷下降,過熱度不斷增大,造成電解槽爐膛破壞、沉淀增多,個別電解槽爐幫較空、大面不結(jié)殼、電流效率明顯下降,能耗大幅上升,為了節(jié)能降耗改變這一現(xiàn)狀我們大膽實踐、不斷更新觀念,重新在生產(chǎn)中摸索實踐了一套適合在復(fù)雜電解質(zhì)體系下高效、低耗生產(chǎn)的技術(shù)條件和運行模式,取得了較為理想的效果。
1 2008年和2013年電解槽運行現(xiàn)狀及控制參數(shù)對比
2007年300kA系列正式投產(chǎn),2009年初經(jīng)濟(jì)危機(jī)停槽,2009年6月二次啟動20萬噸達(dá)產(chǎn),截止2014年已經(jīng)運行近8年。從表1可以看出電解質(zhì)成分鋰含量、鉀含量、鈣含量大幅上升,槽溫度急劇下降,造成初晶溫度大幅下降,平均初晶溫度890℃,過熱度上升,操控機(jī)對氧化鋁濃度控制較差,氧化鋁濃度一直維持在3--3.5%之間高位運行,電解槽有一半出現(xiàn)爐底大量沉淀、爐膛不規(guī)整、爐底壓降急劇上升、極距壓縮電壓擺動、個別電解槽中縫不結(jié)殼,電流效率由以往的93.5%下降到2013年的91.5%,電解槽管理難度加大,能耗大幅上升,直流電耗上升了近400kwh/t-Al,這與節(jié)能降耗主旨格格不入,公司由基礎(chǔ)入手組織廠部骨干制定電解槽技術(shù)條件優(yōu)化方案。
表1 各項參數(shù)對比情況

2 加強(qiáng)電解槽精細(xì)化操作管理
2.1 工藝操作與工藝技術(shù)條件的關(guān)系
正確處理技術(shù)條件與操作質(zhì)量的關(guān)系,確保技術(shù)條件的平穩(wěn)。任何事物都有決定其發(fā)生、發(fā)展的主要矛盾,以及決定其本質(zhì)矛盾的主要方面,鋁電解生產(chǎn)的主要矛盾指工藝技術(shù)條件的平穩(wěn)保持與電解操作質(zhì)量之間相互信賴相互轉(zhuǎn)化的矛盾。簡單地說,對鋁電解生產(chǎn)而言,工藝技術(shù)條件是基礎(chǔ),操作質(zhì)量是保證。只有做到工藝技術(shù)條件的平穩(wěn)持久保持、操作質(zhì)量的高水平,電解生產(chǎn)才能高效低耗平穩(wěn)持久進(jìn)行,反之,無論是操作質(zhì)量出了問題,還是工藝技術(shù)條件發(fā)生了波動都將導(dǎo)致電解槽效率降低,能耗增高。鋁電解生產(chǎn)矛盾的主要方面是保持穩(wěn)定的技術(shù)條件,技術(shù)條件穩(wěn)定的槽子其往往有平衡自調(diào)節(jié)能力強(qiáng)、抗病抗干擾能力強(qiáng)的優(yōu)勢,甚至短時間內(nèi)操作質(zhì)量粗獷也不致誘發(fā)病槽;技術(shù)條件保持不平穩(wěn)的槽子自平衡能力差,較敏感和脆弱,微小的干擾也會導(dǎo)致其發(fā)病,經(jīng)濟(jì)指標(biāo)也一落千丈。作業(yè)質(zhì)量和技術(shù)條件互相影響互為信賴,哪一方面出現(xiàn)問題都將影響電解槽經(jīng)濟(jì)指標(biāo)。為確保工藝條件管理的核心地位,推行工藝技術(shù)條件標(biāo)準(zhǔn)化,力求電解槽的平穩(wěn),堅決杜絕管理者為了短期內(nèi)的經(jīng)濟(jì)指標(biāo)提升而破壞技術(shù)條件匹配,如果隨意更改電解槽的技術(shù)條件將會對電解槽的平穩(wěn)運行埋下隱患,最終導(dǎo)致大病槽發(fā)生,從而大幅度降低經(jīng)濟(jì)指標(biāo),車間對技術(shù)條件保持進(jìn)行嚴(yán)格監(jiān)督和考核,督促技術(shù)條件保持平穩(wěn),在平穩(wěn)技術(shù)條件的同時我們也加強(qiáng)了作業(yè)質(zhì)量,實行操作質(zhì)量全員管理,使操作質(zhì)量管理制度化[1]。工藝技術(shù)條件的平穩(wěn)保持需要高質(zhì)量的操作,同時高質(zhì)量的操作又促進(jìn)了工藝技術(shù)條件的平穩(wěn)保持。
2.2 加強(qiáng)各項操作管理
操作質(zhì)量的重要性顯而易見,抓操作質(zhì)量是僅次于工藝技術(shù)管理的另一件大事,因此,針對目前電解槽現(xiàn)狀規(guī)范了作業(yè)程序、細(xì)化作業(yè)質(zhì)量,通過加強(qiáng)工人技術(shù)比武有力提高了工人作業(yè)技術(shù)水平,并把作業(yè)質(zhì)量管理制度化,加強(qiáng)監(jiān)督、評比、考核,極大提高了工作質(zhì)量,目前大面收邊整形、卡具壓降、導(dǎo)桿打磨、16h電流分布測量、封極評比己成為當(dāng)班必須進(jìn)行的工作。同時加大換陽極對爐底沉淀、結(jié)殼的人工處理,彌補(bǔ)電解槽低溫狀態(tài)下爐底不干凈的現(xiàn)狀。
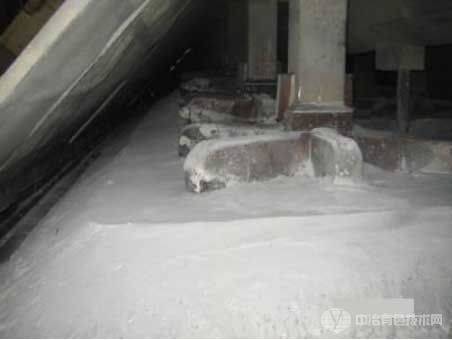
圖1 電解槽大面規(guī)整
3 加強(qiáng)過熱度的控制建立和規(guī)整爐膛
3.1 調(diào)整電解質(zhì)的可控成分,提高電解質(zhì)的初晶溫度
表2 每1%添加劑對初晶溫度的影響

由于鋰鹽、鉀鹽、鈣鹽的影響造成電解槽初晶溫度不斷減小,電解槽爐幫融化,氧化鋁溶解能力顯著降低,為了有效提高槽溫、減小電解槽過熱度我們適當(dāng)提高了分子比,分子比由2008年的2.35提高到目前的2.90,整整提高了0.55個點。
其次,加強(qiáng)氧化鋁濃度的控制,由于電解質(zhì)成分變化較大,沈陽院2005年設(shè)計的操控機(jī)已經(jīng)不能滿足目前超低溫生產(chǎn)的需要,2013年底我廠和中南工大聯(lián)合開發(fā)了一套更加智能的適應(yīng)超低溫條件下對氧化鋁濃度控制的新型操控機(jī)。2014年初操控機(jī)全部更新?lián)Q代完畢,實際測量氧化鋁濃度控制在1.5-2.5%之間,控制效果較為理想。較以前對比氧化鋁濃度控制下降了1%,氧化鋁濃度的進(jìn)一步降低為初晶溫度的提高創(chuàng)造了有利條件,因為我們知道每1%的氧化鋁濃度影響電解質(zhì)初晶溫度大約在10度左右。
最后,通過大修停槽統(tǒng)計在產(chǎn)鋁量明顯較少,由于二次啟動槽在超低溫情況下運行8年以后爐底沖蝕坑較多,爐底結(jié)殼、沉淀相對較多,2013年通過對20臺大修電解槽抽出在產(chǎn)鋁統(tǒng)計,平均在產(chǎn)鋁在21.8噸左右,明顯較少,于是人為通過半年逐步調(diào)整鋁水平,鋁水平由2008年的26cm提高的目前的30cm,有效增大了電解槽的在產(chǎn)鋁量,2014年大修停槽鋁量都在25-26噸,在產(chǎn)鋁量的加大有效減少了過熱度,同時對電解槽的穩(wěn)定性有很大的提高,電解槽針擺大幅度下降。
加大進(jìn)口氧化鋁的使用比例,2013年下半年為了遏制鋰、鉀、鈣的進(jìn)一步升高,廠部果斷決定使用進(jìn)口氧化鋁每天按20%的比例打入料倉,半年后鋰、鉀、鈣有緩慢下降的趨勢。
表3 調(diào)整以后和以前技術(shù)條件對比
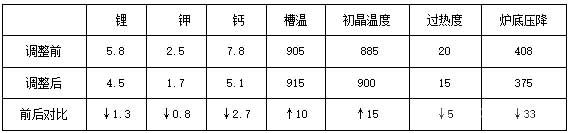
通過以上三個方面的調(diào)整,2014年初實測電解槽初晶溫度提高了近15度,過熱度下降了5度,15度的過熱度時間證明在超低溫電解情況下能夠較好的維持電解槽平穩(wěn)、高效運行。由于過熱度得到了控制。加之操控機(jī)更換后氧化鋁濃度控制更低,電解槽爐幫逐步長厚,厚度 達(dá)到15cm,爐底沉淀逐步減少,電解槽爐底壓降逐步降低,極距進(jìn)一步增大,電解槽穩(wěn)定性和電效取得明顯提高。
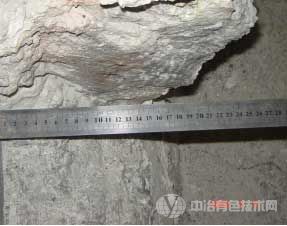
圖2 技術(shù)條件調(diào)整后大修電解槽刨爐爐幫厚度圖
4 在陽極電流密度不變情況下增加陰極電流密度
我廠300kA電解槽在設(shè)計時中縫寬度較寬,達(dá)到180mm,為了在不影響電解槽極距和平穩(wěn)運行前提下強(qiáng)化電流降低電壓,最后決定對陽極進(jìn)行靠中縫側(cè)進(jìn)行加長10mm,最后A、B兩面陽極靠中縫側(cè)長度共加長了20mm,電解槽中縫寬度由原來的180mm變?yōu)楝F(xiàn)在的160mm,電流由兩次強(qiáng)化到了308kA,這樣陽極電流密度幾乎不變情況下,把陰極電流密度由0.733提高到了接近0.74。電解槽運行更加平穩(wěn)、高效。
5 新型開槽陽極技術(shù)的應(yīng)用
從國外大型預(yù)焙電解槽提高效率的經(jīng)驗來看,近年來普遍采用了陽極開槽技術(shù),一是可使陽極底掌下的氣膜破裂,利于陽極氣體外排,降低陽極壓降,增大陽極導(dǎo)電截面,并強(qiáng)化電流生產(chǎn),提高電流效率;三是氣泡在陽極底部停留時間的減少和電解質(zhì)流場的改進(jìn)有利于降低陽極效應(yīng)系數(shù),可延長陽極使用周期。通過對國內(nèi)陽極生產(chǎn)技術(shù)的了解和對洛陽豫港龍泉鋁業(yè)有限公司300KA電解槽技術(shù)特性分析,結(jié)合以往開槽經(jīng)驗對開槽進(jìn)行了改進(jìn),以往開槽的高度兩端一致,改為靠中縫端開16cm,靠大面開12cm,這樣盡量讓陽極氣體排向中縫,保證爐幫不受電解質(zhì)的過量攪動而減薄,又增加了中縫下料點氧化鋁的散開、溶解速度。有效降低了陽極氣模壓降,為降低電壓創(chuàng)造了條件。
6 改進(jìn)作業(yè)細(xì)節(jié),降低槽工作電壓,走低壓 電解之路
電解槽各種壓降,是消耗大量電力能源的無底黑洞,這部分電量不但造成了浪費,而且也破壞電解生產(chǎn)的技術(shù)條件平穩(wěn)。
表4 槽電壓設(shè)計分?jǐn)偳闆r

我公司從治理電解槽各種壓降入手,針對電流通過的各個環(huán)節(jié),有針對性的采取相應(yīng)的措施,盡最大程度降低各環(huán)節(jié)壓降值,達(dá)到降低槽工作電壓的目的。由于槽平均電壓的組成中,陽極壓降、槽周母線壓降、分解與極化壓降相對數(shù)值變化不大,視為常數(shù)定值,在日常操作中,從效應(yīng)分?jǐn)倝航?、爐底壓降、電解質(zhì)壓降入手,采取:
①打磨鋁母線和陽極導(dǎo)桿接觸部位,通過增加導(dǎo)電性能,降低鋁母線和鋁導(dǎo)桿接觸壓降。
②對陽極導(dǎo)桿上的突起、溝棱進(jìn)行拋光。
③進(jìn)行技術(shù)改進(jìn),制作封極備極專用料框,加快封極速度,減少電解槽的熱量損失,降低陽極壓降。
通過一些列措施的采取,先后治理了母線與導(dǎo)桿之間的壓降,使之由以前單極20毫伏以上降到現(xiàn)在的單極5毫伏左右;立柱母線壓接點壓降從15mv降至7mv以下。
通過半年對各項技術(shù)條件的調(diào)整目前電解槽運行穩(wěn)定,槽溫由以前的905℃提高到目前的915---918℃,電流效率由91.5%提高到目前的92.8%,平均電壓通過一系列措施目前已經(jīng)降到3.95V以內(nèi),原鋁直流電耗降低到目前的12680kwh/t-Al,與以往相比降低了400kwh/t-Al。
7 結(jié)束語
電解質(zhì)體系的轉(zhuǎn)變已成河南境內(nèi)鋁電解的一個普遍現(xiàn)象,由此引發(fā)的電解槽能耗上升、管理難度增大無疑給目前的電解鋁企業(yè)雪上加霜,但是通過調(diào)整電解槽其他各項技術(shù)條件,遏制鋰鹽進(jìn)一步升高,使其保持在合理范圍之內(nèi)一樣可以取得較好的經(jīng)濟(jì)技術(shù)指標(biāo)。
參考文獻(xiàn)
[1] 邱竹賢.《預(yù)焙槽煉鋁》第三版.冶金工業(yè)出版社,2008.
[2] 李清.《大型預(yù)焙槽煉鋁生產(chǎn)工藝與操作實踐》.中南大學(xué)出版社,2006,P167
[3] 任必軍.《300KA預(yù)焙陽極電解槽槽壽命及其影響因素》.中南工業(yè)大學(xué)出版社,2008.
[4] 洛陽豫港龍泉鋁業(yè)有限公司《生產(chǎn)技術(shù)簡報》.2014年 .
聲明:
“300KA預(yù)焙電解槽在復(fù)雜電解質(zhì)體系下經(jīng)濟(jì)技術(shù)指標(biāo)優(yōu)化” 該技術(shù)專利(論文)所有權(quán)利歸屬于技術(shù)(論文)所有人。僅供學(xué)習(xí)研究,如用于商業(yè)用途,請聯(lián)系該技術(shù)所有人。
我是此專利(論文)的發(fā)明人(作者)