1 前言
赤峰云銅有色金屬有限公司始建于2006年6月,以加工赤峰金峰銅業(yè)有限公司所供給的
陽極銅為原料,年產(chǎn)高純陰極銅10萬噸。2010年1月為了更好地發(fā)展赤峰云銅,由云南銅業(yè)股份公司和赤峰金峰銅業(yè)有限公司進(jìn)行資產(chǎn)整合,其中云南銅業(yè)股份公司占股權(quán)比例65%,金峰銅業(yè)占35%,赤峰云銅受讓了金峰銅業(yè)公司
銅冶煉系統(tǒng)的全部資產(chǎn)以及熱電廠和鐵路專用線,還有幾乎全部的經(jīng)營管理人員和生產(chǎn)技術(shù)人員以及具有國際先進(jìn)水平的金峰雙側(cè)吹熔池熔煉技術(shù)?,F(xiàn)已發(fā)展成為擁有從礦銅—冰銅—粗銅—陽極銅—高純陰極銅以及煙氣制酸全套生產(chǎn)裝置的限上規(guī)模企業(yè),現(xiàn)有實(shí)際產(chǎn)能達(dá)到高純陰極銅12萬噸/年、冶煉煙氣制酸及銷售48萬噸/年、綜合利用銅冶金渣35萬噸/年,工信部2015年第37號(hào)公告公布了符合《銅冶煉行業(yè)規(guī)范條件》企業(yè)名單,赤峰云銅有色金屬有限公司名列其中。
赤峰云銅在整合至今的近5年半的時(shí)間里,憑借原有技術(shù)積累,依托云銅集團(tuán)綜合優(yōu)勢,持續(xù)進(jìn)行了技術(shù)創(chuàng)新,不斷完善了金峰熔池熔煉技術(shù)并取得突破性進(jìn)展,同時(shí)成功開發(fā)了雙爐粗銅連續(xù)吹煉工藝技術(shù)和高濃度SO2煙氣制酸復(fù)合轉(zhuǎn)化技術(shù),促進(jìn)了企業(yè)提質(zhì)增效,提高了清潔生產(chǎn)水平。下面對金峰雙側(cè)吹熔池熔煉技術(shù)的最新進(jìn)展和生產(chǎn)實(shí)踐進(jìn)行簡要介紹。
2 金峰熔池熔煉工藝概述
熔池熔煉工藝根據(jù)氣體噴吹方式可分為三種類型: 即頂吹式熔煉,以艾薩熔煉、澳斯麥特熔煉和三菱熔煉法為代表;側(cè)吹式熔煉,以諾蘭達(dá)熔煉、瓦紐柯夫熔煉法和白銀法熔煉為代表;底吹式熔煉,以水口山煉銅法為代表。因送風(fēng)位置的不同,脫硫脫鐵的反應(yīng)速率和效果均存在差異。金峰雙側(cè)吹熔池熔煉工藝的冶煉機(jī)理與通用的銅冶煉工藝一致,其核心技術(shù)在于熔煉爐的結(jié)構(gòu)和過程控制。
2.1 工藝流程
金峰熔池熔煉工藝流程圖見圖1。

采用DCS集散控制系統(tǒng)實(shí)現(xiàn)工藝過程的監(jiān)視和管理任務(wù),煉銅原料(銅精礦、煙塵、黑銅粉等)、熔劑和燃料(焦粉或原煤)按設(shè)定數(shù)量均勻混合,經(jīng)由主皮帶轉(zhuǎn)輸至爐頂下料口連續(xù)進(jìn)入熔煉爐落入熔池,同時(shí),通過爐體兩側(cè)的風(fēng)道向熔池中鼓入富氧壓縮空氣;在富氧空氣的強(qiáng)烈攪拌和熔池的高溫作用下,煉銅物料與液態(tài)熔體均勻混合并熔化,在熔池內(nèi)熔體、爐料和鼓入氣體三者之間迅速實(shí)現(xiàn)傳質(zhì)傳熱過程,完成造渣、造锍反應(yīng),反應(yīng)形成的冰銅因密度較大而不斷沉降聚集到熔池下部,經(jīng)虹吸道連續(xù)排出、再通過溜槽進(jìn)入連續(xù)吹煉爐(或根據(jù)PS轉(zhuǎn)爐需要間斷放出);熔渣則聚集到熔池上部,形成渣層,經(jīng)電極渣室從排渣口連續(xù)溢流排出,經(jīng)過溜槽進(jìn)入緩冷渣包(或進(jìn)入貧化爐,再經(jīng)水淬進(jìn)入渣池);含SO2的高溫?zé)煔膺B續(xù)穩(wěn)定的進(jìn)入余熱鍋爐回收廢熱,在經(jīng)電收塵進(jìn)入制酸系統(tǒng)。
2.2 金峰雙側(cè)吹熔池熔煉爐的結(jié)構(gòu)
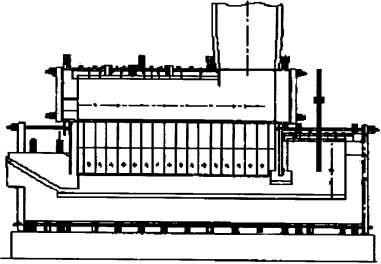
圖2 金峰雙側(cè)吹熔池熔煉爐結(jié)構(gòu)圖
金峰雙側(cè)吹熔池熔煉爐為臥式、長方體,爐體由沉淀分離區(qū)、反應(yīng)區(qū)和煙化區(qū)構(gòu)成,分別設(shè)置在爐體下部、中部和上部;爐頂設(shè)有三個(gè)加料口和煙氣出口;爐體下部偏上兩側(cè)爐壁上平行對稱設(shè)置一次風(fēng)道,爐體中上部兩側(cè)爐壁上設(shè)置二次風(fēng)道;爐體下部的一端設(shè)有冰銅虹吸放出口,另一端設(shè)有電極渣室和熔渣放出口;煙氣出口設(shè)在熔渣放出口端;熔煉爐煙氣出口與余熱鍋爐進(jìn)口由特制煙道連接。
2.3 金峰側(cè)吹熔池熔煉工藝的特點(diǎn)
富氧側(cè)吹熔池熔煉工藝具有如下特性:
(1)流程短,裝備簡單,投資省。以年產(chǎn)100kt/a粗銅的設(shè)計(jì)規(guī)模為例,金峰熔煉工藝的投資僅是澳斯麥特工藝的一半。
(2)雙側(cè)多風(fēng)道鼓風(fēng)。金峰爐在爐兩側(cè)設(shè)置風(fēng)道,在爐體長度受限的情況下,可比單側(cè)(如諾蘭達(dá)爐)設(shè)置得更多(25m2的爐型共可設(shè)置32個(gè)風(fēng)道)。多風(fēng)道送風(fēng)的優(yōu)點(diǎn)是物料攪拌和氧化反應(yīng)更均勻,反應(yīng)更迅速,與單風(fēng)道送風(fēng)(如艾薩/奧斯邁特)相比可減少局部過氧化現(xiàn)象。
(3)吹混合層,氣、液、固三相接觸充分。熔池熔煉爐有的吹冰銅層(如底吹爐),有的吹冰銅層與渣層的混合層(如諾蘭達(dá)法),有的吹渣層(如艾薩、奧斯邁特法);金峰爐吹混合層,其優(yōu)點(diǎn)是大部分富氧空氣直接與新進(jìn)物料接觸,使氧化傳質(zhì)過程縮短,渣型適應(yīng)性強(qiáng),不但氧化反應(yīng)速度快,而且也能減少銅和鐵的氧化和過氧化現(xiàn)象。
(4)熔渣與冰銅在爐內(nèi)實(shí)現(xiàn)分離。爐內(nèi)熔體溫度高,熔池深度高達(dá)2300mm,不但渣銅分離效果好,而且在渣銅分離過程中,新形成的大量冰銅雨通過渣層,對渣層中的冰銅小顆粒有洗滌聚合作用,可有效降低渣中的冰銅含量,金屬直收率高。
(5)原料的適應(yīng)性強(qiáng)。爐料無需深度干燥、細(xì)磨、造粒等特殊處理,含水≤10%的銅精礦物和粒度≤20mm的塊礦、粒度≤35mm的熔劑可直接入爐;燃料適應(yīng)范圍廣,無煙煤、煙煤、焦粉、天然氣均可作為燃料,而且固體燃料無需加工、直接配料入爐。
(6)熔煉強(qiáng)度大,操作彈性寬泛。由于送風(fēng)部位的爐壁采用水冷銅水套和采用不銹鋼、紫銅復(fù)合送風(fēng)嘴,耐高溫耐氧化,故可采用高濃度富氧空氣(含氧60~95%)鼓風(fēng),熔煉強(qiáng)度大,自熱性更強(qiáng),更節(jié)省能源。芒特艾薩、奧斯邁特、諾蘭達(dá)、白銀爐等由于受風(fēng)槍和爐體壽命的限制,富氧濃度只能到55%左右。床能力為55~95t/d?m2,單系統(tǒng)粗銅生產(chǎn)能力可達(dá)100~250kt/a。
(7)綜合能耗低,節(jié)能效果好。燃料率3~5%,粗銅綜合能耗113kgce/tCu。
(8)操作簡單易控,自動(dòng)化程度高。整個(gè)系統(tǒng)配備DCS集散控制系統(tǒng),實(shí)現(xiàn)在線監(jiān)測和遠(yuǎn)程調(diào)控;現(xiàn)場無需打風(fēng)眼作業(yè),熔體排放口及溜槽易于清理,勞動(dòng)強(qiáng)度低;檢修工作量小,單風(fēng)嘴可工作兩年以上,且更換容易,兩人配合、半小時(shí)即可完成。
(9)熔體連續(xù)排放。熔煉產(chǎn)生的冰銅可連續(xù)排出,也可在爐內(nèi)臨時(shí)蓄存、根據(jù)PS轉(zhuǎn)爐吹煉的需要間斷放出,不需要單設(shè)保溫爐;熔煉渣連續(xù)溢流排出。
(10)爐壽長、耐火材料消耗低。爐壽可達(dá)3年以上,爐體易燒損和受沖刷的高溫部位,均采用銅水套冷卻掛渣保護(hù)技術(shù),無需消耗高檔耐火材料;其他部位仍采用耐火磚砌筑,可減少爐體散熱損失。
(11)設(shè)計(jì)合理,安全性能可靠。鍋爐故障不影響冶金爐安全;無運(yùn)動(dòng)部件,因而工作安全可靠;煙氣出口與余熱鍋爐連接煙道采用特殊耐火材料砌筑煙道,既有利于單體硫的進(jìn)一步燃燒,又避免了鍋爐漏水進(jìn)爐可能引起爆炸的安全風(fēng)險(xiǎn)。
(12)無逸散煙氣,環(huán)境友好。爐膛負(fù)壓運(yùn)行,爐體密封性好,漏風(fēng)率小,加料口無煙氣外溢;排渣放銅點(diǎn)的環(huán)集煙氣全部收集匯入制酸系統(tǒng),操作環(huán)境好,可實(shí)現(xiàn)熔煉清潔生產(chǎn)。
3 技術(shù)進(jìn)展
3.1 自造熔池開爐技術(shù)
3.1.1 自造熔池開爐技術(shù)開發(fā)背景
金峰雙側(cè)吹熔池熔煉爐從2008年6月建成投產(chǎn)以來,采用注入熔體開爐法,即開爐過程利用原有閑置鼓風(fēng)爐制造熔體注入金峰爐,作開爐造熔池?zé)岱磻?yīng)引子。此開爐方法不但程序繁瑣,而且開爐設(shè)備維護(hù)及開爐費(fèi)用偏高,同時(shí)存在熔渣過熱不足及單位時(shí)間熱熔渣供量有限的缺點(diǎn),此開爐技術(shù)的不足,正是金峰熔池熔煉爐的不完善之處。由此,自金峰熔池熔煉技術(shù)開發(fā)之初,始終致力于金峰爐自造熔池開爐技術(shù)的探索和研究。
為了降低開爐成本、簡化開爐程序、節(jié)省原始建設(shè)基建投資、完善金峰熔池熔煉技術(shù),赤峰云銅依據(jù)金峰熔池熔煉工藝和裝備特點(diǎn),綜合和借鑒國內(nèi)外冶金爐開爐方法和工程實(shí)踐經(jīng)驗(yàn),于2010年9月10日制定了金峰雙側(cè)吹熔池熔煉爐自造熔池開爐的技術(shù)方案,并確定于2010年9月25日,在年度大修復(fù)產(chǎn)的原始開爐過程中付諸實(shí)施。
3.1.2 自造熔池開爐方案及實(shí)施效果
自造熔池開爐技術(shù)方案實(shí)施的過程控制:熔煉爐按烘爐程序嚴(yán)格控制升溫速率,烘爐末期,逐漸增加木柴投加量,由小火逐步過渡到大火,待木柴達(dá)到一定高度時(shí),酌量均衡投加焦炭,焦炭均勻燃燒且達(dá)到一定厚度,開始分批次定量投加低品位冰銅、投加轉(zhuǎn)爐渣,投料過程中密切跟蹤爐內(nèi)燃燒和渣料熔化狀況,適時(shí)適量提高富氧濃度和鼓風(fēng)壓力。待熔體高度超過風(fēng)眼時(shí),開始投加銅精礦、熔劑和燃料,短時(shí)間即可轉(zhuǎn)入正常生產(chǎn)程序。本技術(shù)采用特殊裝置和措施,徹底解決傳統(tǒng)固體爐料開爐法存在的定點(diǎn)加料布料不均勻、熔池爐缸深而焦炭燃燒不充分、易產(chǎn)生過量CO 引起爆炸等問題。整個(gè)開爐過程,程序簡單、易于操作、時(shí)間短、能耗低,一切順行,未發(fā)現(xiàn)異常情況,達(dá)到了技術(shù)方案設(shè)定的預(yù)期目標(biāo),做到一次開爐成功。
采用自造熔池開爐技術(shù),克服和解決了注入熔體開爐法的費(fèi)用高、耗時(shí)長及傳統(tǒng)固體爐料開爐法存在的布料不勻、溫升不均等缺點(diǎn)和問題,做到開爐耗時(shí)短費(fèi)用低和安全可靠,可達(dá)到開車成功率百分之百;同時(shí),實(shí)現(xiàn)烘爐過程與開爐過程的有效銜接,爐內(nèi)蓄熱和溫升隨開爐過程逐步提高,避免溫度急劇變化對爐窯結(jié)構(gòu)和壽命的影響。與2008年和2009年采用鼓風(fēng)爐制造熔體開爐相比,避免了存在的熱量損失,規(guī)避了熔體吊包轉(zhuǎn)運(yùn)傾倒過程的安全風(fēng)險(xiǎn),縮短了時(shí)間,提高效率,減少了對環(huán)境的污染并降低了勞動(dòng)強(qiáng)度,同時(shí)節(jié)約開爐成本近45萬元/次。兩種開爐技術(shù)的耗材耗時(shí)情況如表1所示。
表1 兩種開爐技術(shù)的對比

3.1.3 推廣應(yīng)用情況
自造熔池開爐技術(shù)于2010年、2011年、2012年、2013年在赤峰云銅的年度大修復(fù)產(chǎn)開爐過程使用,并先后應(yīng)用于四川康熙銅業(yè)、富春江和鼎銅業(yè)熔煉爐的原始開車。實(shí)踐證明,本開爐技術(shù)安全可靠,完善了金峰熔池熔煉技術(shù),為金峰雙側(cè)吹熔池熔煉工藝及裝備的推廣應(yīng)用鋪墊了堅(jiān)實(shí)的基礎(chǔ)。
3.2.1 熔渣電爐貧化
熔煉渣在出渣口經(jīng)溜槽流入貧化電爐,在貧化爐內(nèi)澄清沉淀3.5個(gè)小時(shí),經(jīng)水淬、烘干外銷,其中在熔煉礦量小于65t/h時(shí),貧化爐能滿足正常生產(chǎn)要求,棄渣成分分析數(shù)據(jù),如表2:
表2 貧化后的棄渣成分

隨著金峰側(cè)吹熔池熔煉技術(shù)的日趨成熟,熔煉礦量逐漸增加,與此同時(shí),貧化爐的負(fù)荷也隨之增加,熔渣在貧化爐內(nèi)不能充分沉淀,造成貧化效果不理想,貧化成本增加,產(chǎn)能提升后熔礦量80t/h時(shí),貧化后的棄渣成分分析數(shù)據(jù),如表3所示。
表3 產(chǎn)能提升后的棄渣成分

3.2.2 高鐵渣浮選貧化
自金峰側(cè)吹熔煉技術(shù)的日日臻完善,熔煉礦量不斷增加,為滿足生產(chǎn)需求,經(jīng)深入研究決定對熔煉渣型進(jìn)行調(diào)整,通過全渣浮選代替貧化爐,進(jìn)而實(shí)現(xiàn)提高金屬回收率和銅渣綜合利用的降本增效目標(biāo)。
2008年至2013年末,金峰爐的熔煉機(jī)理獨(dú)特加之采用鐵硅鈣三元系渣型和直流貧化電爐,熔渣含銅可控制在0.5%以下。但是因渣率較高(精礦含銅20%、含鐵27%時(shí),噸粗銅產(chǎn)生渣量達(dá)到3.2t),所以導(dǎo)致渣含銅損失仍較高(約為1.35%)。
要進(jìn)一步降低渣含銅損失,顯然需要從進(jìn)一步降低渣含銅和降低渣率兩方面入手,為此,赤峰云銅提出如下解決方案:
將Fe-SiO2-CaO三元系渣型調(diào)整為Fe-SiO2兩元系渣型,并將硅鐵比由目前的0.9左右調(diào)整到0.5~0.55,從而將渣率由目前的3.2左右降低到2.3左右;使渣量減少約25%。
(2)實(shí)踐證明,按上述工藝方案調(diào)整渣型后,渣含銅將升高到1%左右,且電爐貧化效果甚微;然而,鐵硅比為1.5~2.0的硅鐵渣型比較適合浮選法貧化;所以赤峰云銅提出取消電爐貧化方法,采用浮選法進(jìn)行貧化。渣型調(diào)整前后的運(yùn)行指標(biāo)如表4所示,調(diào)整前后熔渣成分如表5所示。
表4 渣型調(diào)整前后的運(yùn)行指標(biāo)

表5 調(diào)整前后熔渣成分

以上運(yùn)行數(shù)據(jù)表明:
a.鐵硅比越高渣含銅隨之增加,渣中磁性鐵含量也隨之增加,有利于渣選貧化。
b.隨著渣中磁性鐵含量的增加,熔煉渣熔點(diǎn)升高,需要較高的操作溫度。
c.高鐵渣磁性鐵含量增加,在渣沉降區(qū)內(nèi),會(huì)有磁性鐵橫膈膜析出。
d.高鐵渣有利于爐壽的延長,實(shí)踐表明,高鐵渣能起到掛渣護(hù)爐的作用。
經(jīng)過上述分析,金峰爐選擇鐵硅比在1.5-1.7之間的渣型為宜,既不會(huì)導(dǎo)致磁性鐵大量積聚,給操作帶來難度,又不影響渣選貧化效果。
赤峰云銅高鐵硅比熔煉渣浮選浮選尾礦含銅可控制在0.25%以下,依目前銅精礦綜合供應(yīng)情況,按礦產(chǎn)陰極銅110kt/a計(jì)算,調(diào)整渣型后可節(jié)約熔煉成本不低于1050萬元/a、與采用電爐貧化時(shí)期相比可多回收近900t/a、浮選尾礦實(shí)現(xiàn)資源化利用,經(jīng)綜合技經(jīng)測算,實(shí)施調(diào)整渣型浮選貧化后凈利潤不低于2650萬元/a。
3.3 雙爐粗銅連續(xù)吹煉工藝技術(shù)
3.3.1 開發(fā)過程
在金峰富氧雙側(cè)吹熔池熔煉工藝成功實(shí)現(xiàn)工業(yè)化應(yīng)用之后,為解決PS轉(zhuǎn)爐吹煉工藝存在的間斷進(jìn)料、分期作業(yè)、逸散煙氣收集困難處理費(fèi)用高、漏風(fēng)率高、余熱利用差、作業(yè)率低等工藝缺陷和環(huán)保問題,2009年立足高效、節(jié)能、環(huán)保的研發(fā)標(biāo)準(zhǔn),確立了“雙爐粗銅連續(xù)吹煉工藝技術(shù)”研究課題,即根據(jù)PS轉(zhuǎn)爐吹煉工藝技術(shù)的原理,將PS轉(zhuǎn)爐吹煉的造渣期和造銅期兩個(gè)反應(yīng)過程分置在造渣爐和造銅爐內(nèi)連續(xù)進(jìn)行。自2012年開始,赤峰云銅有色金屬有限公司與金峰冶金技術(shù)發(fā)展有限公司合作,借鑒金峰富氧雙側(cè)吹熔池熔煉、頂吹熔池熔煉以及三菱法吹煉和閃速吹煉工藝的技術(shù)經(jīng)驗(yàn),開發(fā)了雙側(cè)吹造渣爐和頂吹造銅爐。在2013年5月至2014年8月期間,本著既不影響正常生產(chǎn)又確保試驗(yàn)裝置安裝、試車順利進(jìn)行的原則,在赤峰云銅火法冶煉生產(chǎn)系統(tǒng)中插入雙爐粗銅連續(xù)吹煉工藝技術(shù)的工業(yè)化試驗(yàn)?zāi)K,利用6個(gè)月時(shí)間實(shí)施了工業(yè)化試驗(yàn)裝置建設(shè),經(jīng)歷8個(gè)月、7次工業(yè)化試驗(yàn)。對歷次試驗(yàn)進(jìn)行總結(jié),改進(jìn)和完善了工藝裝備,在2014年9月6日的第八次試驗(yàn)中取得圓滿成功,經(jīng)系統(tǒng)調(diào)整和修繕,于2014年11月7日一次開車成功、順利實(shí)現(xiàn)工業(yè)化應(yīng)用。
3.3.2 技術(shù)簡介
雙爐粗銅連續(xù)吹煉工藝技術(shù)創(chuàng)造性地將PS轉(zhuǎn)爐吹煉的造渣期和造銅期兩個(gè)反應(yīng)過程分置在雙側(cè)吹造渣爐和頂吹造銅爐內(nèi)連續(xù)進(jìn)行;熔煉爐、造渣爐和造銅爐均采用溜槽連接,實(shí)現(xiàn)了液態(tài)冰銅、白冰銅和粗銅的連續(xù)流動(dòng)轉(zhuǎn)輸;所有溜槽和排接渣點(diǎn)的環(huán)集煙氣100%收集、匯入煙氣制酸系統(tǒng);工藝煙氣分別流經(jīng)余熱鍋爐、產(chǎn)出的飽和中壓蒸汽集中用于余熱發(fā)電;造渣反應(yīng)產(chǎn)出的吹煉渣連續(xù)排出經(jīng)渣包緩冷去浮選貧化;精煉渣、造銅過程的吹煉渣返回造渣爐,電解殘陽極返回造銅爐,冷料處理率100%。通過上述技術(shù)方案的綜合集成,創(chuàng)新性地開發(fā)了由雙側(cè)吹造渣爐和頂吹造銅爐組成的粗銅連續(xù)吹煉系統(tǒng),實(shí)現(xiàn)了粗銅吹煉過程的連續(xù)化。
3.3.3 工業(yè)化應(yīng)用情況
赤峰云銅采用雙爐粗銅連續(xù)吹煉工藝技術(shù)已建成年產(chǎn)粗銅12.5萬噸生產(chǎn)線,生產(chǎn)運(yùn)行穩(wěn)定、易于操作控制,直收率高,吹煉成本低,各項(xiàng)技術(shù)經(jīng)濟(jì)指標(biāo)優(yōu)良。與PS轉(zhuǎn)爐吹煉時(shí)期相比較:產(chǎn)能提高20%;噸粗銅耐火材料成本下降30元/tCu;吹煉煙氣余熱發(fā)電增效58元/tCu;節(jié)省環(huán)集煙氣脫硫處理成本95元/tCu、硫的回收率提高1.3%;工藝煙氣量小且連續(xù)穩(wěn)定、制酸噸酸電耗降低14kwh/tH2SO4;吹煉作業(yè)率由92.5%提高至99%;粗銅綜合能由143kgce/tCu降至113kgce/tCu; 粗銅含硫由0.3%降至0.03%;吹煉渣含銅由4.0%降至2.3%。與清潔生產(chǎn)(HJ558-2010)的一級指標(biāo)和能源消耗限額(GB21248-2014)的先進(jìn)指標(biāo)對比:粗銅含硫<0.03%、達(dá)到≤0.1%要求;爐齡>360d、達(dá)到≥240d要求;廢氣的收集與處理做到了100%收集利用;二氧化硫轉(zhuǎn)化率>99.94%、達(dá)到≥99.8%要求;硫的總捕集率>99.8%、達(dá)到≥98.5%要求;硫的回收率>98.3%、達(dá)到≥97%要求;粗銅單位產(chǎn)品綜合能耗113kgce/tCu,滿足清潔生產(chǎn)(HJ558-2010)一級指標(biāo)≤340kgce/tCu的要求,同時(shí)達(dá)到能源消耗限額(GB21248-2014)中銅冶煉企業(yè)單位產(chǎn)品能耗先進(jìn)值≤150kgce/tCu的指標(biāo)要求。
3.3.4 潛在的推廣價(jià)值
雙爐粗銅連續(xù)吹煉工藝技術(shù)是熔池熔煉技術(shù)的開創(chuàng)性拓展,采用此技術(shù)用既可徹底根除傳統(tǒng)PS轉(zhuǎn)爐吹煉造成的煙氣、煙塵、廢熱逸散,杜絕低空污染,又可有效利用余熱、降低煉銅成本,有效改善吹煉工序作業(yè)環(huán)境,特別是在生態(tài)環(huán)保、節(jié)能減排等法律法規(guī)要求日益嚴(yán)格、標(biāo)準(zhǔn)逐步提高的大趨勢條件下,本工藝技術(shù)均具有突出優(yōu)勢。
該研發(fā)成果,于2014年4月2日“雙爐雙側(cè)吹造渣頂吹造銅連續(xù)吹煉爐”獲得實(shí)用新型專利授權(quán)、并已同日申請發(fā)明專利;于 2015年4月23日“雙爐粗銅連續(xù)吹煉工藝技術(shù)”通過由中國有色金屬協(xié)會(huì)組織的科技成果鑒定,認(rèn)為該工藝技術(shù)投資低、節(jié)能減排效果好、經(jīng)濟(jì)和社會(huì)效益顯著,可實(shí)現(xiàn)銅冶煉清潔生產(chǎn),同時(shí)技術(shù)經(jīng)濟(jì)指標(biāo)先進(jìn),整體技術(shù)達(dá)到國際先進(jìn)水平,建議加快推廣應(yīng)用。
4 結(jié)語
從赤峰云銅及浙江和鼎銅業(yè)采用金峰熔池熔煉技術(shù)的生產(chǎn)運(yùn)行情況看,各項(xiàng)經(jīng)濟(jì)技術(shù)指標(biāo)均非常理想。此技術(shù)投資省、建設(shè)周期短,流程簡單、自動(dòng)化程度較高,操作彈性寬泛、簡單易控,備料簡單、原料適應(yīng)性強(qiáng),綜合能耗低、運(yùn)行成本低,無逸散煙氣、噪音低、環(huán)境友好,該熔池熔煉工藝的單系列可達(dá)到年處理銅精礦100萬噸以上規(guī)模,輔以雙爐粗銅連續(xù)吹煉技術(shù)的應(yīng)用,粗銅綜合能耗可降至115kgce/tCu以下,在環(huán)保、能耗、運(yùn)行成本、建設(shè)投資均具有突出優(yōu)勢,同時(shí)隨著金峰熔池熔煉技術(shù)和雙爐粗銅連續(xù)吹煉工藝技術(shù)的日臻完善,可實(shí)現(xiàn)全流程連續(xù)煉銅,進(jìn)而形成一套嶄新的銅冶煉清潔生產(chǎn)技術(shù)。
聲明:
“金峰雙側(cè)吹熔池熔煉技術(shù)進(jìn)展” 該技術(shù)專利(論文)所有權(quán)利歸屬于技術(shù)(論文)所有人。僅供學(xué)習(xí)研究,如用于商業(yè)用途,請聯(lián)系該技術(shù)所有人。
我是此專利(論文)的發(fā)明人(作者)