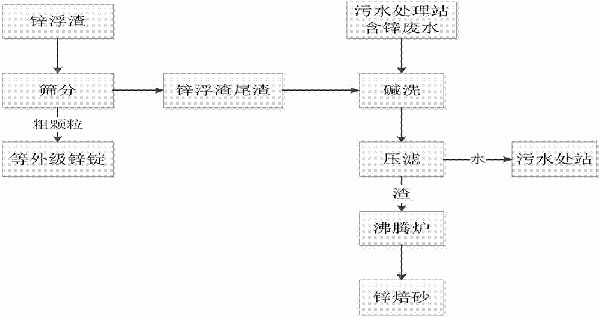
本發(fā)明涉及濕法鋅冶煉技術(shù)領(lǐng)域,尤其涉及一種鋅浮渣回收利用方法。
背景技術(shù):
目前,我國75%以上的鋅是采用
濕法煉鋅工藝生產(chǎn)出來的。在濕法煉鋅過程中,副產(chǎn)出一定數(shù)量的鋅浮渣,其是電積的陰極鋅澆鑄成為鋅錠過程中形成的氧化鋅并夾帶一定數(shù)量的金屬鋅顆粒形成的渣。這種氧化渣由于夾帶部分的鋅,使鋅的熔鑄收率降低,為了提高陰極電積鋅片的熔鑄直收率,在熔鑄過程中還加入少量的氯化銨,目的是將包裹鋅的氧化鋅破壞,使鋅熔化進(jìn)入鋅錠中,提高鋅的直收率。陰極鋅片熔鑄過程中所產(chǎn)生的鋅浮渣主要含鋅、氧化鋅和氯化鋅。由于鋅浮渣中含有較高的氯(一般在1~4%),因此不能直接返回濕法鋅治煉流程在回收其中的鋅,否則使浸出液、凈化液和電積液中的氯離子含量升高,使電積鋅產(chǎn)品中的鉛含量增高,影響鋅錠產(chǎn)品的質(zhì)量。
電解鋅鑄錠過程產(chǎn)生的鋅浮渣含氯1~4%、鋅78~86%,已列入國家危險(xiǎn)
固廢目錄,目前行業(yè)內(nèi)存在以下幾種通用的處置方法:(1)進(jìn)入揮發(fā)窯生產(chǎn)次氧化鋅后生產(chǎn)電解鋅;(2)直接進(jìn)入電解鋅浸出,浸出液進(jìn)行離子交換(或萃取)脫氯;(3)直接外賣后用于生產(chǎn)氯化鋅等產(chǎn)品;(4)葫蘆島鋅業(yè)股份有限公司有專利使用鋅浮渣生產(chǎn)鋅粉、西北礦冶研究院有專利使用鋅浮渣利用“浸出+萃取”技術(shù)生產(chǎn)電解鋅、寶山鋼鐵股份有限公司有專利使用鋅浮渣生產(chǎn)鋅合金?!敖?萃取(離子交換)脫氯”存在鋅損失大、
污水處理量大、酸堿用量大的成本與環(huán)保問題;鋅浮渣進(jìn)入揮發(fā)窯生產(chǎn)次氧化鋅后現(xiàn)生產(chǎn)電解鋅需要投資成本高。
因此,實(shí)有必要提供一種改進(jìn)的鋅浮渣回收利用方法。
技術(shù)實(shí)現(xiàn)要素:
本發(fā)明的主要目的在于提供一種首先篩分回收粗鋅粒、再用含鋅廢水(150-180mg/l)和雨水的混合物堿洗回收粗鋅粒后的鋅浮渣,反應(yīng)完成后分離堿洗反應(yīng)漿得到濾渣和濾液,濾渣再和鋅精礦一起焙燒脫氯,氯含量從1-4%下降至0.15%以下,同時(shí)可回收含鋅廢水中65%以上的鋅,濾液中的鋅含量降至50mg/l,在提高鋅的回收率同時(shí)降低了污水站處理成本。
為實(shí)現(xiàn)上述目的,本發(fā)明提供一種鋅浮渣回收利用方法,其特征在于,所述鋅浮渣回收利用方法包括如下步驟:
步驟一、初步篩分鋅浮渣獲得粗鋅粒,粗鋅粒用于生產(chǎn)鋅錠,剩余鋅浮渣尾渣進(jìn)入下一工序;
步驟二、利用電鋅廠含鋅廢水和雨水的混合液堿洗所述鋅浮渣尾渣,反應(yīng)完成后壓濾堿洗反應(yīng)漿得到濾液和濾渣,堿洗反應(yīng)漿的ph值為8~8.5;
步驟三、高溫焙燒所述濾渣和鋅精礦的混合物脫氯,氯含量降低至0.15%以下。
在本發(fā)明提供的所述的鋅浮渣回收利用方法一較佳實(shí)施例中,所述粗鋅粒為粒徑大于2毫米的鋅粒。
在本發(fā)明提供的所述的鋅浮渣回收利用方法一較佳實(shí)施例中,所述步驟一中用于初步篩分的裝置為雷蒙機(jī)、球磨機(jī)或重力搖床。
在本發(fā)明提供的所述的鋅浮渣回收利用方法一較佳實(shí)施例中,所述步驟二中堿洗反應(yīng)時(shí)間為1~3小時(shí),堿洗反應(yīng)溫度為常溫。
在本發(fā)明提供的所述的鋅浮渣回收利用方法一較佳實(shí)施例中,所述步驟二中加入碳酸鈉調(diào)節(jié)堿洗反應(yīng)漿的ph值。
在本發(fā)明提供的所述的鋅浮渣回收利用方法一較佳實(shí)施例中,所述步驟二中含鋅廢水和雨水的混合液的ph值為5.0~6.0,含鋅150~180mg/l。
在本發(fā)明提供的所述的鋅浮渣回收利用方法一較佳實(shí)施例中,所述步驟二中含鋅廢水和雨水的混合液的加入量為10m3/噸鋅浮渣尾渣。
在本發(fā)明提供的所述的鋅浮渣回收利用方法一較佳實(shí)施例中,所述步驟三中高溫焙燒裝置為沸騰爐或揮發(fā)窯。
在本發(fā)明提供的所述的鋅浮渣回收利用方法一較佳實(shí)施例中,所述步驟三中焙燒溫度為880~920℃。
相對于現(xiàn)有技術(shù),本發(fā)明提供的一種鋅浮渣回收利用方法具有以下有益效果:
一、初步篩分回收粗鋅粒生產(chǎn)等外級(jí)電解鋅,設(shè)備采用雷蒙機(jī)、球磨機(jī)或重力搖床均可,設(shè)備投資與生產(chǎn)工藝簡單、成本低,該部分粗鋅粒占鋅浮渣總鋅的30~45%,使電解鋅增產(chǎn)0.7%以上,減少每噸鋅能耗與產(chǎn)成本。
二、用電鋅廠含鋅廢水和雨水堿洗鋅浮渣回收鋅并脫氯,①不增加污水處理量,與用清水堿洗次氧化鋅等含鋅物料相比,堿量增加量<10%;②回收了含鋅廢水和雨水65%以上的含鋅,使污水含鋅由150-180mg/l下降至50mg/l以下,提高了電解鋅廠鋅利用率和降低了污水處理站污水處理成本;③鋅浮渣尾渣含氯總量由1.5~3%下降至0.4%以下,實(shí)現(xiàn)了脫氯的目的,提升了鋅浮渣的價(jià)值。
三、堿洗脫氯后的鋅浮渣進(jìn)一步進(jìn)入沸騰爐與鋅精礦一起搭配高溫焙燒進(jìn)一步脫除氯離子,氯離子含量降至0.15%以下,符合電解鋅鋅焙砂質(zhì)量標(biāo)準(zhǔn),使鋅浮渣實(shí)現(xiàn)由
危廢變成鋅焙砂的增值,且焙燒后的爐渣進(jìn)入浸出工序后不會(huì)導(dǎo)致溶液含氯量增加。
附圖說明
圖1為本發(fā)明鋅浮渣回收利用方法一較佳實(shí)施例的步驟流程圖;
圖2為本發(fā)明鋅浮渣回收利用方法一較佳實(shí)施例的工藝流程圖。
本發(fā)明目的的實(shí)現(xiàn)、功能特點(diǎn)及優(yōu)點(diǎn)將結(jié)合實(shí)施例,參照附圖做進(jìn)一步說明。
具體實(shí)施方式
應(yīng)當(dāng)理解,此處所描述的具體實(shí)施例僅僅用以解釋本發(fā)明,并不用于限定本發(fā)明。
下面將結(jié)合本發(fā)明實(shí)施例中的附圖,對本發(fā)明實(shí)施例中的技術(shù)方案進(jìn)行清楚、完整地描述,顯然,所描述的實(shí)施例僅僅是本發(fā)明的一部分實(shí)施例,而不是全部的實(shí)施例?;诒景l(fā)明中的實(shí)施例,本領(lǐng)域普通技術(shù)人員在沒有作出創(chuàng)造性勞動(dòng)前提下所獲得的所有其他實(shí)施例,都屬于本發(fā)明保護(hù)的范圍。
需要說明,本發(fā)明實(shí)施例中所有方向性指示(諸如上、下、左、右、前、后……)僅用于解釋在某一特定姿態(tài)(如附圖所示)下各部件之間的相對位置關(guān)系、運(yùn)動(dòng)情況等,如果該特定姿態(tài)發(fā)生改變時(shí),則該方向性指示也相應(yīng)地隨之改變。
另外,在本發(fā)明中如涉及“第一”、“第二”等的描述僅用于描述目的,而不能理解為指示或暗示其相對重要性或者隱含指明所指示的技術(shù)特征的數(shù)量。由此,限定有“第一”、“第二”的特征可以明示或者隱含地包括至少一個(gè)該特征。在本發(fā)明的描述中,“多個(gè)”的含義是至少兩個(gè),例如兩個(gè),三個(gè)等,除非另有明確具體的限定。
在本發(fā)明中,除非另有明確的規(guī)定和限定,術(shù)語“連接”、“固定”等應(yīng)做廣義理解,例如,“固定”可以是固定連接,也可以是可拆卸連接,或成一體;可以是機(jī)械連接,也可以是電連接;可以是直接相連,也可以通過中間媒介間接相連,可以是兩個(gè)元件內(nèi)部的連通或兩個(gè)元件的相互作用關(guān)系,除非另有明確的限定。對于本領(lǐng)域的普通技術(shù)人員而言,可以根據(jù)具體情況理解上述術(shù)語在本發(fā)明中的具體含義。
另外,本發(fā)明各個(gè)實(shí)施例之間的技術(shù)方案可以相互結(jié)合,但是必須是以本領(lǐng)域普通技術(shù)人員能夠?qū)崿F(xiàn)為基礎(chǔ),當(dāng)技術(shù)方案的結(jié)合出現(xiàn)相互矛盾或無法實(shí)現(xiàn)時(shí)應(yīng)當(dāng)認(rèn)為這種技術(shù)方案的結(jié)合不存在,也不在本發(fā)明要求的保護(hù)范圍之內(nèi)。
本發(fā)明提供一種鋅浮渣回收利用方法,所述鋅浮渣為濕法煉鋅過程中的副產(chǎn)物,具體為電積的陰極鋅澆鑄成為鋅錠過程中形成的氧化鋅并夾帶一定數(shù)量的金屬鋅顆粒形成的渣含氯量為1~4%,含鋅量為78~86%,已列入國家危險(xiǎn)固廢目錄。本發(fā)明首先篩分回收粗鋅粒、直接將粗鋅粒用于等外級(jí)鋅錠生產(chǎn),剩余鋅浮渣尾渣再用含鋅廢水(150-180mg/l)和雨水的混合物堿洗回收回收鋅和脫氯,反應(yīng)完成后分離堿洗反應(yīng)漿得到濾渣和濾液,濾渣再和鋅精礦一起焙燒脫氯,氯含量從1~4%下降至0.15%以下,同時(shí)可回收含鋅廢水中65%以上的鋅,濾液中的鋅含量降至50mg/l。
具體地,請參閱圖1和圖2,本發(fā)明提供的濕法煉鋅凈化除雜方法包括如下步驟:
步驟s10、初步篩分鋅浮渣獲得粗鋅粒,粗鋅粒用于生產(chǎn)鋅錠,剩余鋅浮渣尾渣進(jìn)入下一工序;
所述鋅浮渣為濕法煉鋅過程中的副產(chǎn)物,具體為電積的陰極鋅澆鑄成為鋅錠過程中形成的氧化鋅并夾帶一定數(shù)量的金屬鋅顆粒形成的渣含氯量為1~4%,含鋅量為78~86%。在本實(shí)施例中,通過雷蒙機(jī)、球磨機(jī)或重力搖床初步篩分粒徑大于2毫米的鋅粒直接生產(chǎn)等外級(jí)鋅錠,該部分粗鋅粒占鋅浮渣總鋅的30~45%,使電解鋅增產(chǎn)0.7%以上,減少每噸鋅能耗與產(chǎn)成本。
步驟s20、利用電鋅廠含鋅廢水和雨水的混合液堿洗所述鋅浮渣尾渣,反應(yīng)完成后壓濾堿洗反應(yīng)漿得到濾液和濾渣,堿洗反應(yīng)漿的ph值為8~8.5;
本發(fā)明利用電鋅廠含鋅廢水和雨水的混合液堿洗鋅浮渣尾渣,加入碳酸鈉調(diào)節(jié)堿洗反應(yīng)漿的ph值至8~8.5,堿洗反應(yīng)溫度為常溫,堿洗反應(yīng)時(shí)間為1~3小時(shí)。鋅浮渣尾渣中的氯化鋅、含鋅廢水中的鋅離子與碳酸鈉發(fā)生反應(yīng)生成氯化鈉和碳酸鋅,氯化鈉溶于水,碳酸鋅不溶于水,通過壓濾機(jī)固液分離后,氯化鋅中的鋅和含鋅廢水中的鋅沉積在濾渣中,而鋅浮渣尾渣中的氯離子則在濾液中,因此,鋅浮渣尾渣中的氯含量降低,可從1.5~3%下降至0.4%以下,而含鋅廢水中的鋅可回收65%以上。具體地,濾渣進(jìn)入下一工序,濾液返回污水處理站進(jìn)行再處理。
在本實(shí)施例中,含鋅廢水和雨水的混合液的ph值為5.0~6.0,含鋅150~180mg/l;濾液中的鋅含量為50mg/l。
優(yōu)選地,含鋅廢水和雨水的混合液的加入量為10m3/噸鋅浮渣尾渣,碳酸鈉的加入量為40千克/噸鋅浮渣。
步驟s30、高溫焙燒所述濾渣和鋅精礦的混合物脫氯,氯含量降低至0.15%以下。
將濾渣和鋅精礦放入沸騰爐或揮發(fā)窯中880~920℃高溫焙燒得到鋅焙砂,鋅焙砂的氯含量降至0.15%以下,符合電解鋅鋅焙砂質(zhì)量標(biāo)準(zhǔn),使鋅浮渣實(shí)現(xiàn)由危廢變成鋅焙砂的增值,且焙燒后的爐渣進(jìn)入浸出工序后不會(huì)導(dǎo)致溶液含氯量增加。
本發(fā)明提供的鋅浮渣回收利用方法工藝簡單,投資少,脫氯方法簡單,在將鋅浮渣變成合格鋅焙砂實(shí)現(xiàn)增值的同時(shí)還回收了含鋅廢水中的鋅,生產(chǎn)成本低且增值效果好。
實(shí)施例1
將氯含量2.352%、鋅含量74.46%、重4噸的鋅浮渣加入雷蒙機(jī)初步篩分,得到0.8噸粗鋅粒和3.10噸的鋅浮渣尾渣,將其中的1.5噸鋅浮渣尾渣加入18m3的攪拌槽內(nèi),加入15立方米的含鋅廢水(含鋅165mg/l)和雨水的混合液及40千克碳酸鈉,常溫下攪拌,攪拌速度為60r/min,堿洗反應(yīng)漿的ph值8.2,反應(yīng)時(shí)間為1.5小時(shí)后,壓濾得到濾渣和濾液,濾渣重量為1.98噸,水份為30%,濾液含鋅量43mg/l返為回污水處理站進(jìn)行處理,濾渣加入到鋅精礦中一起放入沸騰爐中焙燒得到爐渣,焙燒溫度為900℃,焙燒后的得到的鋅焙砂含氯量為0.06%。
實(shí)施例2
將氯含量2.552%、鋅含量73.46%、重4噸的鋅浮渣加入雷蒙機(jī)初步篩分,得到0.8噸粗鋅粒和3.10噸的鋅浮渣尾渣,將其中的1.5噸鋅浮渣尾渣加入18m3的攪拌槽內(nèi),加入15立方米的含鋅廢水(含鋅165mg/l)和雨水的混合液及40千克碳酸鈉,常溫下攪拌,攪拌速度為60r/min,堿洗反應(yīng)漿的ph值8.1,反應(yīng)時(shí)間為3小時(shí)后,壓濾得到濾渣和濾液,濾渣重量為1.99噸,水份為30%,濾液含鋅量42mg/l返為回污水處理站進(jìn)行處理,濾渣加入到鋅精礦中一起放入沸騰爐中焙燒得到爐渣,焙燒溫度為900℃,焙燒后的得到的鋅焙砂含氯量為0.09%。
以上僅為本發(fā)明的優(yōu)選實(shí)施例,并非因此限制本發(fā)明的專利范圍,凡是利用本發(fā)明說明書及附圖內(nèi)容所作的等效結(jié)構(gòu)或等效流程變換,或直接或間接運(yùn)用在其他相關(guān)的技術(shù)領(lǐng)域,均同理包括在本發(fā)明的專利保護(hù)范圍內(nèi)。
技術(shù)特征:
技術(shù)總結(jié)
本發(fā)明公開了一種鋅浮渣回收利用方法。所述鋅浮渣回收利用方法包括如下步驟:步驟一、初步篩分鋅浮渣獲得粗鋅粒,粗鋅粒用于生產(chǎn)鋅錠,剩余鋅浮渣尾渣進(jìn)入下一工序;步驟二、利用電鋅廠含鋅廢水和雨水的混合液堿洗所述鋅浮渣尾渣,反應(yīng)完成后壓濾堿洗反應(yīng)漿得到濾液和濾渣,堿洗反應(yīng)漿的pH值為8~8.5;步驟三、高溫焙燒所述濾渣和鋅精礦的混合物脫氯,氯含量降低至0.15%以下。本發(fā)明提供的鋅浮渣回收利用方法在脫除鋅浮渣中氯的同時(shí)回收了含鋅廢水中的鋅,工藝簡單,成本低且增值效果好。
技術(shù)研發(fā)人員:趙均瑞;龍玉高;石明忠;龍敏;石建平;羅來光
受保護(hù)的技術(shù)使用者:湖南三立集團(tuán)股份有限公司
技術(shù)研發(fā)日:2017.09.07
技術(shù)公布日:2018.01.09
聲明:
“鋅浮渣回收利用方法與流程” 該技術(shù)專利(論文)所有權(quán)利歸屬于技術(shù)(論文)所有人。僅供學(xué)習(xí)研究,如用于商業(yè)用途,請聯(lián)系該技術(shù)所有人。
我是此專利(論文)的發(fā)明人(作者)